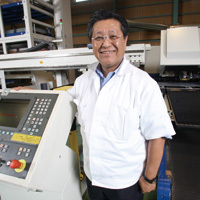
Photo by Toshiaki Usami
埼玉県所沢市、畑が広がる閑静な住宅街の一角に、大手メーカーの設計開発や部品調達担当者が日参する企業がある。金属加工の井口一世だ。
従来、金型を使って作るほかなかった金属製品を、同社では金型を使わず、穴開けや曲げといった板金加工で作る「金型レス生産」をウリにする。
大量生産には金型を使う製造が向いているが、周知のとおり、大量生産はコストの低い海外に生産シフトしている。
一方、試作品や少量生産品、高度な技術を必要とする製品は国内生産が主流だ。高価な金型が不要なら、メーカーは初期投資や準備期間が大幅に抑えられる。また、たとえば円形製品は金型で作ると20%以上の材料ロスが出るが、板金加工ならゼロに近い。
「数が2000個以下なら、金型生産に比べ3分の1~5分の1のコストダウンが可能」と社長の井口一世は胸を張る。
とりわけ注目されるのが、修理部品生産だ。たとえばコピー機は2000点以上の部品で構成されるが、販売を終了したモデルでも修理部品を7年間は提供しなくてはならない。自動車も同様で期間は15年、部品数は3万点もある。メーカーにとってどの種類をどれくらい作ればいいか読めないのに、膨大な数の部品在庫や金型管理は頭の痛い問題だ。「うちに頼んでくれれば金型を使わずにタイムリーに提供できる」と強気だ。
家業を継ぐも経営危機に
IT知識を武器に起死回生を挑む
「子ども時分は勉強した記憶がほとんどない」という井口は立教大学の付属小学校からエスカレーターで進学、恵まれた環境で育った。
しかし社会に出てからは、思いもしなかった苦労を味わうことになる。新卒で入った計測器メーカーを1年で退社後、実家の金型プレス業を手伝い始めてわずか3ヵ月で父が急死。想定よりもずいぶん早く家業を継ぐことになったのだ。
「右も左もわからない状態から先輩職人に技術を学び、周囲の助けを得ながらなんとか経営を続けた」が、時代の流れには逆らえなかった。大量生産を前提とした仕事は中国に流れてゆき、事業は危機に瀕した。
「生き残るにはどうしたらいいのか──」。日本のモノづくりの将来を考えた結論が金型レスなどのニーズだった。
ただ、アイディアをかなえるには金型生産と同等、もしくはそれ以上の品質のものを板金加工だけで作る技術が必要だ。
井口は欧州へ飛んだ。日本にはない高性能レーザーマシンを見るためだ。
秘策はあった。じつは学生時代から「3~4日徹夜は当たり前で没頭する」ほどのコンピュータおたくで、独学でプログラミングを身につけていた。