ビジネスの「デジタル化」とは、人工知能(AI)やIoT(モノのインターネット)などに関する先端的な技術を活用して、既存のビジネスを変革したり、新たなビジネスを生み出すこと。経済産業省が推進する「デジタル・トランスフォーメーション(DX)」は、デジタル化の推進により従来のビジネスや組織を変革し、新たな付加価値を生み出すことを目指す。そこで早い時期からDXを推進し、現場のスマート化を達成し、さらにその先を目指している先進企業のソニーセミコンダクタマニュファクチャリングと中部電力のケースを取り上げ、現場がどのように変革したのかを、経産省の取り組みを含めてお伝えする。
その1 ソニーセミコンダクタマニュファクチャリング
半導体生産プロセスをデジタルの“目”で見守り
歩留まり100%を目標とするスマートファクトリーを構築
ソニーセミコンダクタマニュファクチャリングは熊本県に本社を置き、半導体の設計・開発・製造からカスタマーサービスまでをトータルで提供する企業だ。半導体製造の各工程をデジタルの“目”で見守る仕組みを構築し、不良品発生前に修正をかけることで、歩留まり100%を目指す。
「話はシンプルなのです」と前置きして、同社IS製品部門部門長の松野知之氏は半導体生産プロセスをこう説明する。
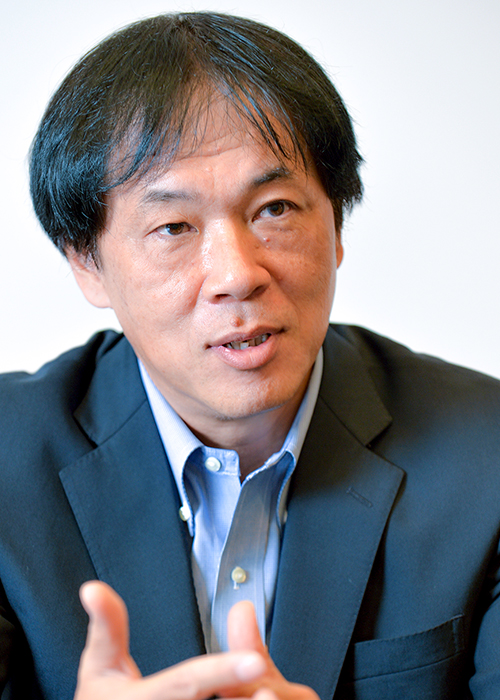
マニュファクチャリング
IS製品部門 部門長
松野知之氏
半導体は、原材料であるシリコンウエハーに複数の膜を積層成膜しながら微細な加工物を作り、製品化に向けての製造プロセスを経て出荷に至る。
「鍵となるのは生産設備です。半導体は設備産業といわれるほど、ものすごくたくさんの設備がある。私が在籍する熊本テクノロジーセンターでは、口径300ミリのシリコンウエハーを原材料として、数百台の装置(工程)を経て製品に仕上げ、最後のテスト工程で顧客が要求するスペックを満たしているかどうかをチェックします」
例えばシリコンウエハーの上にSiO2(二酸化ケイ素)という膜をつける作業では、直径300ミリウエハー全体に均一に、指定した膜質、膜厚のものを成膜しなければならない。これを確認するために、製造ラインでは、IQC(Incoming material Quality Control、部材受入検査)、IPQC(In-line Production QC、工程内検査)などのデータをチェックし、問題がなければ次の工程に送る作業を繰り返していく。
このとき膜厚に問題が生じていれば、なぜそうなったのかを追求し、例えば原因が成膜装置の温度やガスの流量の変動があったということを突き止めたのなら、そこを修正する。一つの製品は25枚単位でつくるので、1枚目で異変に気付くことができれば24枚は正常なものになるし、1枚目の製造中に異変に気付いて修正ができれば「不良品はでません。工程・作業を安定化、改善する取り組みを進めています」(松野氏)。
しかも装置は24時間稼働しており、数百もある各設備の処理はコンマ数秒単位で変化しているので、「職人技をもってしても対処ができない」(松野氏)。また収集するデータが膨大な量(ビッグデータ)になるため、クラウドコンピューティングでは通信や処理に時間がかかりすぎる。
「そこで設備にエッジコンピューティング(設備の近くでデータを処理する)の考え方を取り入れて、小さな異変を検知した時点で、オンタイムで設備に修正をかける仕組みづくり」(松野氏)を急いでいる。
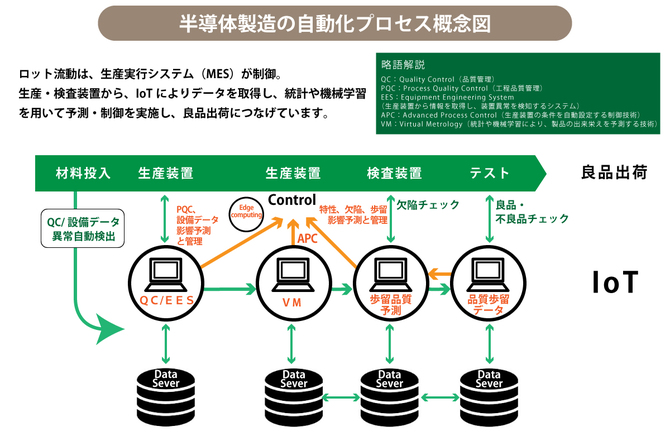
半導体生産プロセスは、材料投入から生産装置、検査装置、テスト、良品出荷という数百工程を経る。このそれぞれの工程でIoTによりデータを取得し、エッジコンピューティング技術を用いて小さな異変をキャッチし、修正を行い、不良品ゼロを目指す。(資料提供:ソニーセミコンダクタマニュファクチャリング)
拡大画像表示
「不良品を確認してからフィードバックをかけるのではなく、ビッグデータを分析して源流から修正をかけていくので、不良品を出さずに製品を生産でき、歩留まり(収率)は100%に近付きます」(松野氏)
同社が構築しつつあるスマートファクトリーは巨大な構想(ここで取り上げたケースはほんの一部に過ぎない)であり、社外には公にできないノウハウの塊でもある。
2016年から本格的に取り組みをスタートさせ、完成は2020年代後半になる。そのときには激しい競争を繰り広げている米国勢や韓国勢を抑えて、日本の半導体産業が再びトップに立つことが期待できる。