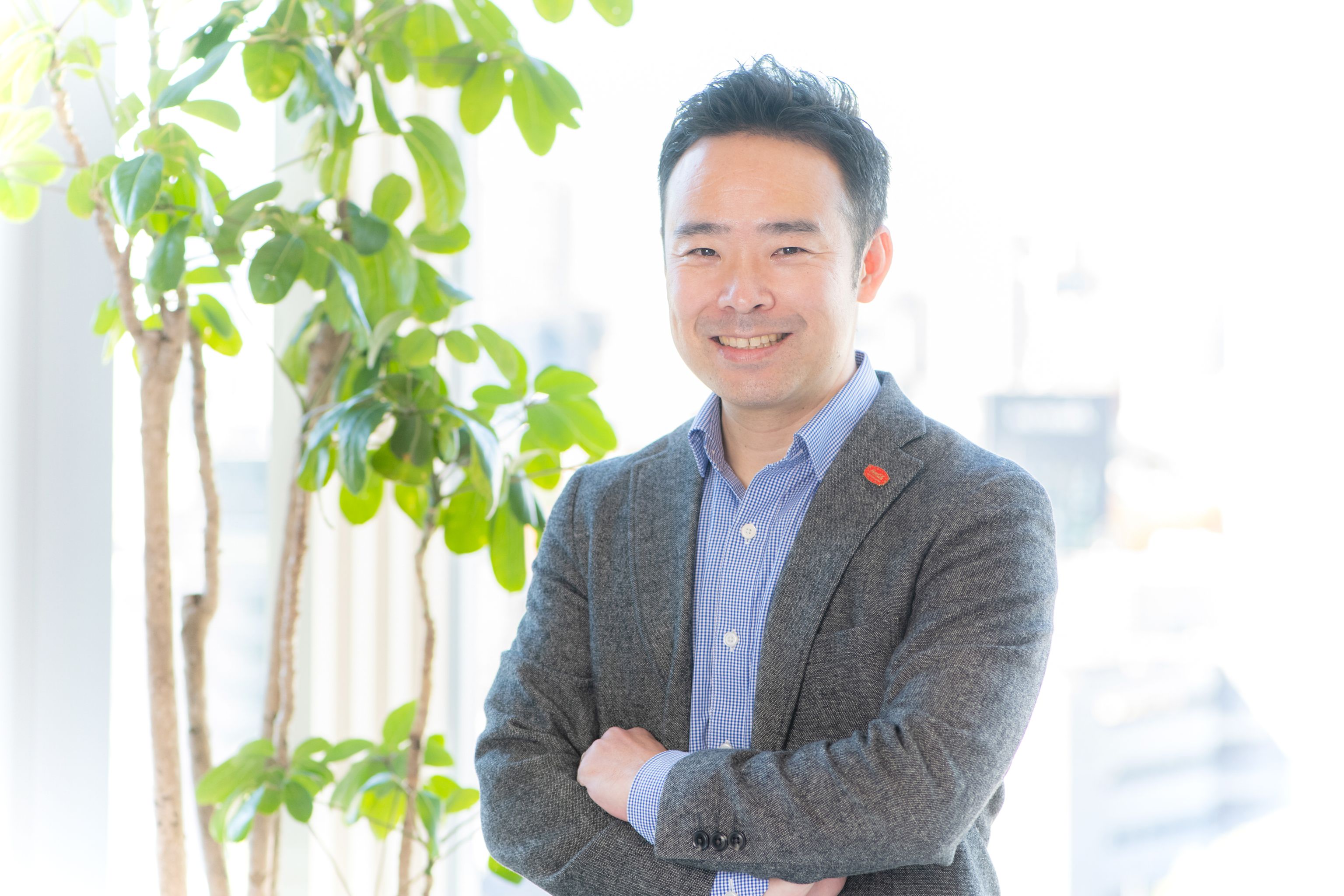
もともと12社の傘下にあった17工場にIoTを導入、標準モデルに統一してDX(デジタルトランスフォーメーション)を実現する――。清涼飲料水・アルコール飲料の製造、加工および販売を行うコカ・コーラ ボトラーズジャパン(CCBJI)で、巨大なDXプロジェクトが進行している。「目的は業務の効率化」だと話す同社製造DX推進課の熊谷直仁課長に、CCBJI流の製造現場改革手法を聞いた。
それぞれ独自のシステムを使用、運営をしていた12の会社が統合
コカ・コーラ ボトラーズジャパン(以下「CCBJI」)は日本の各地域にあった12のボトラー社が統合を経て2017年4月に誕生した。国内1都2府35県の営業地域を持ち、世界に225以上あるコカ・コーラ ボトラーの中でも売上高でアジア最大級という巨大企業だ。
コカ・コーラ社製品を製造する工場は、宮城県の蔵王工場から宮崎県のえびの工場まで営業地域に17ある。それぞれ単独では優れた工場だが「もともと12社のボトラーにひも付いた製造工場なので、それぞれ運営方針は違っていたし、製造設備の機能は同じでも、設備サプライヤーの違いや機械の新旧の違いなどがあり、まったく同じという工場は一つもなく、業務効率化の基本となる標準化が課題でした。最も違っていたのは、現場の製造に対する『考え方』でした」
そう振り返るのは、CCBJIの製造部門でDX推進の指揮を執る熊谷直仁課長だ。
17工場の製造に対する考え方はどれも正しい
日本のコカ·コーラシステムは、原液の供給と製品の企画開発やマーケティング活動を行う日本コカ·コーラと、製品の製造・販売などを担う、CCBJI を含む五つのボトラー会社および関連会社で構成されている。このコカ・コーラシステムは世界共通の「KORE(Coca-Cola Operating Requirements)」と呼ぶ独自のマネジメントシステムによるオペレーション管理を行っている。品質、食品安全、環境、労働安全衛生に関する基準を網羅した厳しいものだ。
KOREに担保されて、最終的に出荷される製品の味や品質に各ボトラーで違いはないが、「過去から蓄積された経験やいろいろな変遷を経て、そこに至る考え方に違いが生まれていたのです」。登山に例えるなら、目指す頂上は一つだが、登山ルートが工場によって違うということ。その大きな理由はこうだ。
「工場が増えていく過程は通常、一つの工場の生産能力が限界に達すると新工場を建設するという枝分かれの形ですが、当社の場合は、すでにある工場のいろいろな考え方を擦り合わせながら統合していく形でした。そのため、まずは製造現場を標準化する必要性がありました」
そこでまずIoTの導入によって業務の効率化を図る改善活動から手を付けた。改善活動を進める上で熊谷課長は、旧来のやり方を否定しなかった。
「長い歴史の中で、その工場では『正解』とされているやり方があるわけですから、それを頭から否定して強引に統一したのでは現場が混乱してしまいます」
では、各工場の旧来のやり方を否定せずに、いかにして全17工場の製造工程を標準化するのか。次ページからは、CCBJIが取り組んだDX推進、標準化への道のりを紹介する。