各工場の考え方を「強み」と捉える
熊谷課長の製造統括部チームは、現場が結成した受け入れチームと連携してIoTを導入し、業務改善をサポートする姿勢に徹した。そして、17工場の『正解』を強みと受け止め逆手に取った。
「先ほど例に挙げた枝分かれした工場では『正解』が一つなので、他社の工場を研究しない限り、『気付き』を得にくいです。当社は、統合により17工場それぞれの『正解』を比較することができるので、現場が『気付き』を得ることで、“いいとこ取り”ができるのです。業務の効率化が実現すれば、働き方改革にもつながり、現場にメリットがあると説明しました」(熊谷課長)
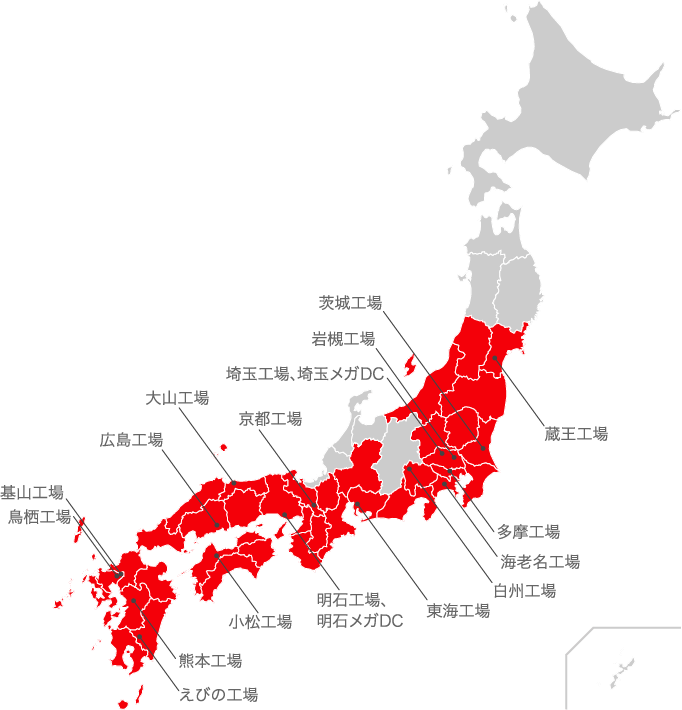
標準化のモデル工場には三つの機能を装備
標準化のモデル工場は、20年6月1日に稼働した広島工場(広島県三原市)だ。約260億円を投じ、約9万㎡の敷地に建つ最新鋭の工場は、ペットボトル製品のアセプティック(無菌充塡)ライン2ラインを備え、1分間に900本(小型ペット)の製造能力を持つ。
熊谷課長は、「まず広島工場から始めて、中期計画に合わせて17工場に広げていく計画」だと言うが、そこには高いハードルがある。それが先述した設備サプライヤーの違いや機械の新旧の違いだ。
「そこで標準化は、17工場の折り合いがつくかどうかを重視して進めています。(熊谷課長が所属する)製造統括部の中でも、品質、製造、メンテナンス、管理といった部門の課長主体でチームをつくり、意見を擦り合わせています。やはりいろいろな制約があるので、今ある設備を上手に使い、最新のやり方に変えて、少しでもモデル工場に近づけていきたいです」
モデル工場のIoTシステムには、次の三つの機能を持たせている。
①ペーパーレス
②遠隔監視
③製造の主要KPIの自動計算
ペーパーレスは、品質の担保や工程の管理に不可欠な日報の作成作業の軽減に役立っている。手書きの時代は日報を毎日平均300枚ほど書かなければならず、日ごとのオペレーションの4分の1を占めていた。その作業を軽減するため、設備とデータと電子帳票を連携させ、情報をワンタップで取得する機能を付加したところ、工場の平均で必要なデータの30%ほどが自動で取り込めるようになった。手書きでは起こりがちな誤記や記入漏れもなくなった。
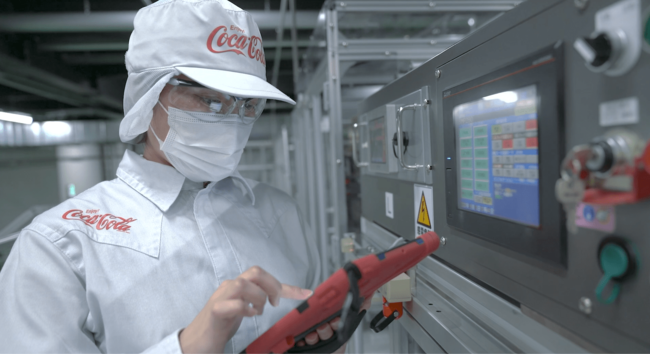
しかも手書きの時代は、担当者が日報をファイリングして書庫に保管し、監査などで製造状況の振り返りが必要なときは、ファイルを探して、該当箇所を見つけ出すという面倒な作業を強いられていたが、「ペーパーレスによって、簡単に検索できるようになりました。日報作成は品質管理上必ずやらなければならない重要な作業ですが、いくら時間をかけて作成しても生産性向上に貢献することがないので、現場の担当者は作業負担の軽減を喜んでいます」と熊谷課長は語る。