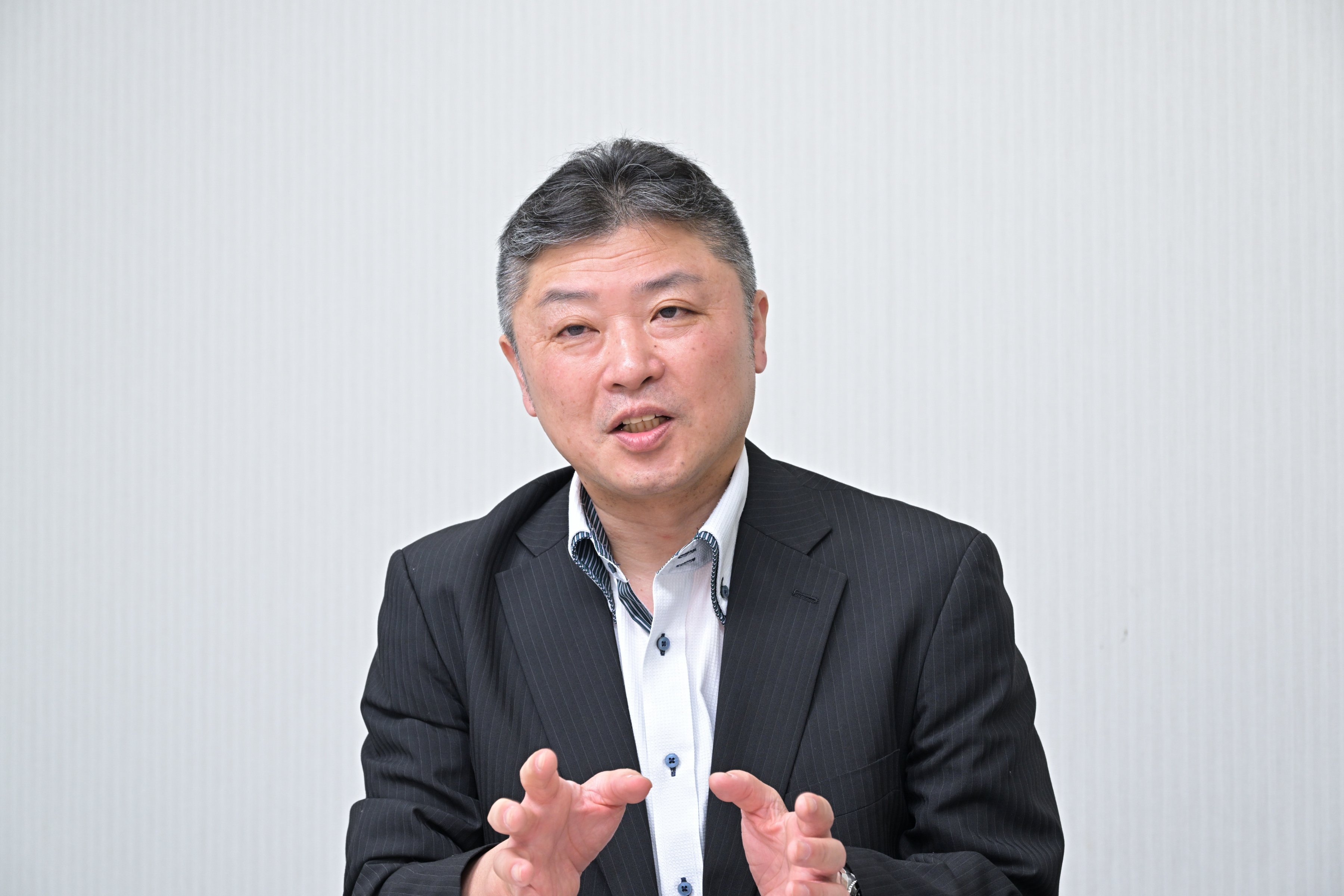
奥野 敦
代表取締役社長
半導体製造装置用の部品や精密機械の製造でプレゼンスの高い三幸。近年は産学連携を展開し、製造業のDX化にも積極的だ。現在は名古屋大学と京都大学発のベンチャー企業と組み、FZ(浮遊帯域溶融)法を利用したFZ法装置(結晶成長炉)の自動操業を実現する装置のプロトタイプ開発プロジェクトに取り組んでいる。技術の核となるのは、製造プロセスの自動化を実現するAI制御アルゴリズムの開発だ。
三幸の設立は1969年。当初はカーボン製品や半導体製造装置用部品などを取り扱う商社としてスタートしたが、顧客ニーズやマーケットの課題に応えるために、2000年代からモノづくりへの挑戦をスタートした。現在、事業の3本柱となっているのは、カーボン、セラミックス、精密機械製品の製造である。カーボンやセラミックスの主力製品は、半導体製造装置の加熱工程で使われるもの、精密機械製品も半導体製造向けの装置やユニットであり、いずれの製品も半導体需要の高まりを背景に、堅調な業績推移を見せている。
熟練のオペレーターが操業する
「FZ法」の自動化を目指す
その三幸が今、チャレンジしているのが、自動操業が可能な結晶成長装置の開発プロジェクトである。ベースとなる装置は、「FZ法装置(結晶成長炉)」。主に半導体シリコンウエハーの材料となるシリコン(ケイ素)の単結晶インゴットを作る炉である。
シリコンウエハーとは半導体の「基板」となる素材で、円柱状になっているシリコンの単結晶インゴットを、厚さ1ミリメートル程度にスライスして使用する。単結晶インゴットは通常、多結晶シリコンを原料として「CZ(チョクラルスキー)法」によって製造される。CZ法とは、るつぼ内で融解した多結晶シリコンの液面に種結晶シリコン棒を漬け、回転させながら引き上げる方法で、種結晶と同じ原子配列をした単結晶インゴットを作ることができる。
一方、今回のベースとなる結晶成長炉で採用されているのは、浮遊帯域溶融(Floating zone melting)法。すなわち、「FZ法」である。これは、棒状の原料(多結晶シリコン)の一部を、高周波や集光加熱によって溶融することで“液体状”の溶融帯を形成し、溶融帯の下部に形成される結晶を降下させることによって、単結晶インゴットを育成する方法だ。手法的には、ろうそくを一度溶かして下部に新しい形状のろうそくを作るのに似ている。
FZ法は空中での作業になるため、CZ法に比べて不純物が入りにくく高純度の単結晶インゴットを作ることができる。ただし、製造に手間がかかるのが難点となっている。
三幸の奥野敦社長は、FZ法装置の課題についてこう説明する。
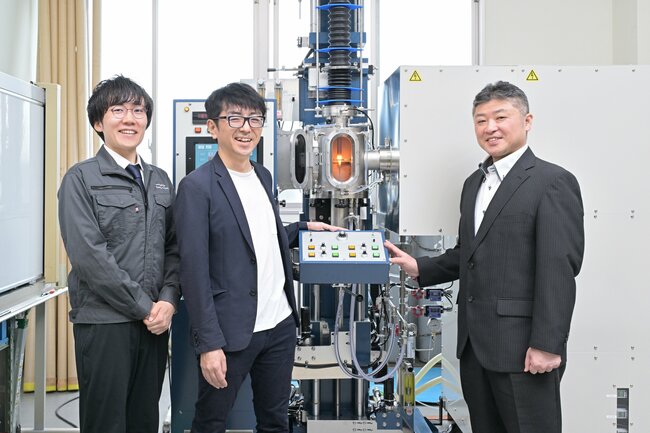
三幸の富山工場にあるFZ法装置の前にて。浮遊帯域溶融(FZ)法による結晶成長プロセスの自動化をシミュレーションで実証する産学連携は、三幸の迅速な対応でスムーズに進捗している
「FZ法は、基本的に熟練のオペレーターが手動で作業を行っています。単結晶インゴットを育成するためには、溶融帯を表面張力によって保持しながら、ネッキングと呼ばれる口径制御を行う必要があるのですが、溶融帯を保持しながらネッキングを行うには、その状態に合わせて、結晶の降下速度や出力を適切に調整することが求められます。つまり操業には、熟練した“職人”の経験や技術が必要になるため、自動化ができないという課題があるのです。今回のプロジェクトは、その属人的な操業をAIを利用して自動化することで、単結晶インゴットの製造を“職人”に頼らず効率的に行えるようにする目的があります」