高速化や安全性を
支えるコア技術
信頼を支えているのは、100年にわたる軸受作りで培ってきた摩擦や摩耗に関する豊富な知見などを基にしたコアテクノロジーだ。
「用途ごとに最適な設計を追究し、試験と解析を極限まで繰り返して性能や安全性を確認します。鋼材や潤滑剤のグリースについても、それぞれの用途に合ったものを自社開発しています」(松原専務)
日本精工の高速鉄道用軸受は、時速500キロ以上の試験にも耐えるほどだという。
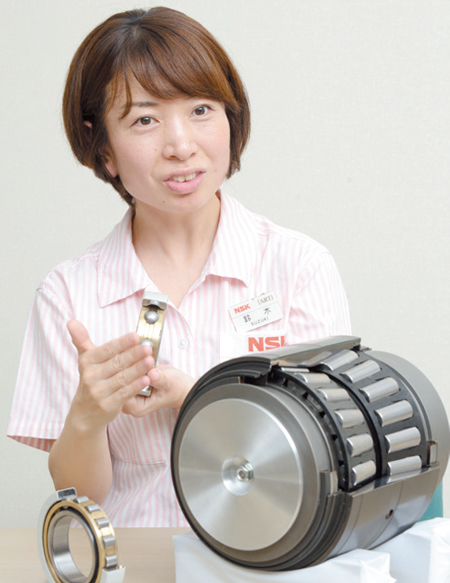
耐久性を高める一方で、小型・軽量化も進めてきた。車軸用軸受の重量を初代新幹線と最新のN700系新幹線で比べると、81キログラムから23キログラムへと、3分の1以下になった。軸受は小型・軽量化するほど摩擦損失を低減できる。また周辺部分も小型化することができ、車両の軽量化につながり、高速化に対応しやすくなる。つまり、同社による軸受の技術革新は、高速鉄道のスピードアップに大きく貢献してきたのである。
その他、「センサー軸受」は、軸受の状態をセンサーが常に監視する製品だ。安全性の向上やメンテナンス周期の延長などのメリットがもたらされる。さらに、センサーから収集された情報を基に軸受の異常を未然に予測する「NSK軸受異常診断システム」も開発している。
このように、軸受の製品力の高さだけでなく、安全確保のための仕組みやメンテナンス、アフターサービス体制まで万全に整えているのが日本精工の強みといえる。新幹線のみならず、海外でも高速鉄道や在来線、地下鉄などで同社の軸受が数多く採用されている理由はここにある。
松原専務は「世界の鉄道用軸受のスタンダードであるEN規格への対応、グローバルな安定供給体制の確立など、海外事業拡大に向けての布石は着実に打っています」と、新幹線で培った技術と信頼を武器に、海外展開をさらに積極的に推し進める構えだ。