この企業は大手製造メーカーで、半導体を中心に部材供給が逼迫する中、部材調達のリードタイムが長期化していました。半年から1年先に納入される部材を発注することが常態化しており、リスクを伴う高額の先行投資をしている状態でした。
そこで、キャッシュの視点から、経営判断として投資の意思決定を行うことにしました。具体的には、販売、生産、調達などのS&OP(セールス・アンド・オペレーション)データの基盤を整備し、これを財務・会計データとつなげて財務インパクトをシミュレーションできるようにしました。これによって、事業計画とサプライチェーン計画を同期化し、財務インパクトを考慮した生産・購買の意思決定を行うことにしました。CFO部門も参加する毎月の製販調整会議で判断を下します。
コーポレート部門がサプライチェーンの意思決定に関与することで、事業計画の透明性が高まり、キャッシュの確保につながることが期待されます。
太田 経営レベルの意思決定を行うには、原材料を調達してから製品をお客様に納品するまでのモノの流れ、それに付随する各種の情報の流れ、そしてキャッシュの流れという三つのレイヤーを可視化する必要があります。
その上で、どういう軸で最適化を図るのかは、企業ごとの戦略やその時々の事業環境によって変わりますから、いろいろな軸で柔軟にシミュレーションできることが重要です。
当社ではそのような仕組みをつくるために、各種のデータを一括して保存・管理・加工できる基盤を構築し、その基盤上でさまざまな予測を出せるAIエンジンを開発したいと考え、活動しているところです。
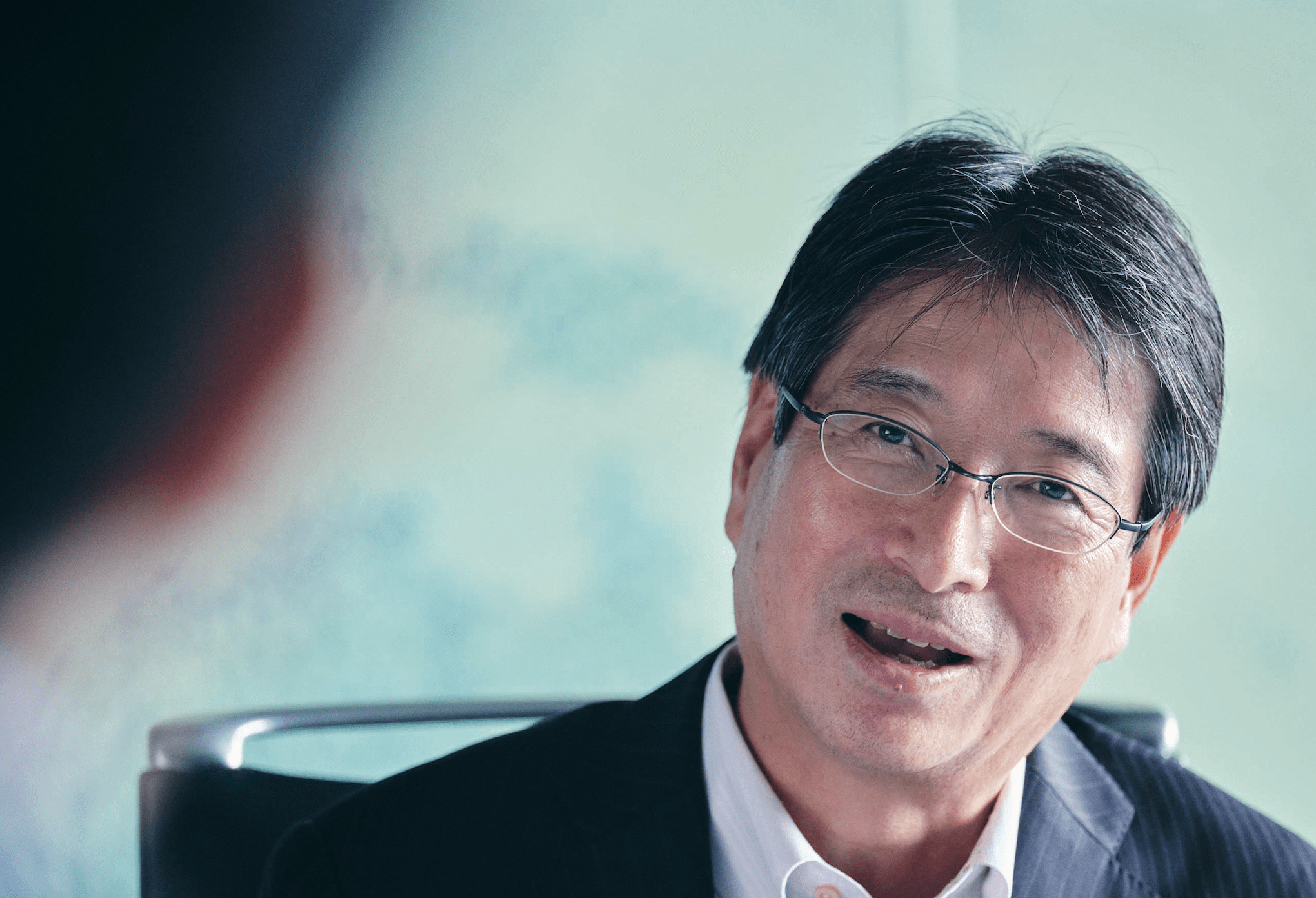
日本のものづくりの強みを活かす規格化・標準化
山中 次にご紹介するのは輸送機器メーカーの事例です。国内に複数の旗艦工場があるのですが、工場ごとに生産・調達・物流のシステムが異なり、同じ工場内でもサプライチェーンデータが各所に散在している状況でした。
そこで、生産、販売、調達、受注・出荷、原価管理などの生産基盤システム、加えて工場のMES(製造実行システム)をグローバル標準となっているパッケージで統一することにしました。同時に、BOM(部品表)やBOP(工程表)などの生産マスターデータも、グローバル標準のデータモデルを活用して統一しました。
非競争領域では、将来の産業プラットフォーム構想も見据えて規格化・標準化を進めることが重要です。これだけでも、部分最適が多く残る日本の工場ではハードルが高い現実があります。
一方、日本のものづくりの強みを活かしきることも同じように重要です。本事例では、JIT(ジャスト・イン・タイム)の納入指示を部品サプライヤーと連携させる情報基盤も整備しました。グローバル標準のパッケージでは実現が難しい、時間単位での組立順序計画やJIT納入指示、ロケーション単位での部品在庫管理を実現し、日本のものづくりの優位性を堅持しています。
太田 当社の場合は、既存の生産基盤システムやMESを一気に刷新するのではなく、既存システムの一つ上のレイヤーにデータ連携基盤を構築し、そこにすべてのデータを吸い上げるアプローチを考えています。このデータ連携基盤を介して、サプライヤーを含む外部とのデータ連携を図ることを構想しています。
産業プラットフォームの構築の取り組みとして始めたのが、建築用ガラスの工事積算工程です。国内の建築用ガラス業界では、工事店と卸売店がガラスの品種や数量、見積もりなどの情報をメールやファクスでやり取りしています。当社の子会社が開発したガラス工事積算システムは、クラウドを介して工事店と卸売店がシームレスにデータ連携でき、当社の基幹システムとも連携できます。これにより、手入力業務の削減、見積作業の時間短縮、入力ミスの防止など、サプライチェーン全体の業務効率化が可能になります。
こうしたデータ連携基盤を他の事業や業務領域でもどんどん構築していきたいと思っています。
デジタルツインでサプライチェーンを再設計する
山中 三つ目の事例としてご紹介するのは、物流企業です。この企業は、コロナ禍の影響で大きく人流が変わり、それに伴う物流の変化に追随できていませんでした。いわゆる物流の2024年問題(トラックドライバーの時間外労働の上限規制)に伴う人手不足とコスト増という構造的な問題も抱えており、効率的な物流ネットワークの再構築が求められていました。
従来は担当者の経験に基づいて物流の分析や対策の立案を行っていたのですが、デジタルツイン技術を活用して、サプライチェーンを再設計できる仕組みを導入しました。デジタル空間で物流拠点の配置や配送ルートをシミュレーションし、配送コストやリードタイムなど多面的な切り口で定量的に評価した上で、リアル空間の物流ネットワークを再編するプランをまとめ上げたのです。
パンデミックや地政学リスク、各国の規制・法制の変更など、突如として供給網が寸断されるリスクが高まっています。物流企業のみならず、グローバルでサプライチェーンを展開する企業にはデジタルツイン技術を活用し、自社の供給網を再設計・再構築できる能力が欠かせないと思います。
太田 当社は化学品プラントの運転状態のデータを取り込み、デジタル空間上でリアルタイムに再現する仕組みを開発しました。すでにインドネシアで運用を始めています。運転状態を可視化したことで、計器や設備の異常を早期に検知できるようになるなど、安定操業に大きな効果を発揮すると期待しています。
また、板ガラスの原料を融解する高温のフロート窯内部の状態をデータで把握し、コンピューター上で再現したり、シミュレーションしたりできる技術も開発しています。今後は、シミュレーションに基づいた効率的な生産体制の構築や温室効果ガス(GHG)削減への活用を図っていく予定です。
こうしたデジタル技術を使ったシミュレーションを広げていくには、現場社員のデジタルスキルを高める必要があり、そのための人材育成に注力しているところですが、最近注目しているのは大規模言語モデル(LLM:自然言語処理の分野で使用されるAI)です。
プログラミングやデータサイエンスの知識がない社員でも、チャット形式でAIと対話しながら、最適化する要件を定めて、シミュレーションできるようになれば、DXのスピードが格段に速まるのではないかと考えています。実際にLLMを活用したインターフェースの開発、検証に着手したところです。
サプライヤーとの情報共有は「QCD+3E」
山中 最後にサプライヤーとの情報連携の高度化に取り組んでいるケースをご紹介します。情報機器メーカーの事例です。
サステナビリティの実現に向けてサプライヤーと共有すべき情報を、当社では「QCD+3E」と定義しています。品質・コスト・納期に関する情報に加えて、三つのE、つまりCO2排出量や水使用量などの環境関連情報、人権や労働環境、紛争鉱物など倫理的な情報、災害などの緊急事態対応に関する情報です。
このメーカーでは、スコープ3(自社のGHG直接排出と電気などの使用に伴う間接排出以外の、事業活動に伴うすべての間接排出)までのカーボンニュートラルを視野に、ティア3(第3次)までのサプライヤーとQCD+3Eの情報を共有できるデータ基盤の構築を目指しています。
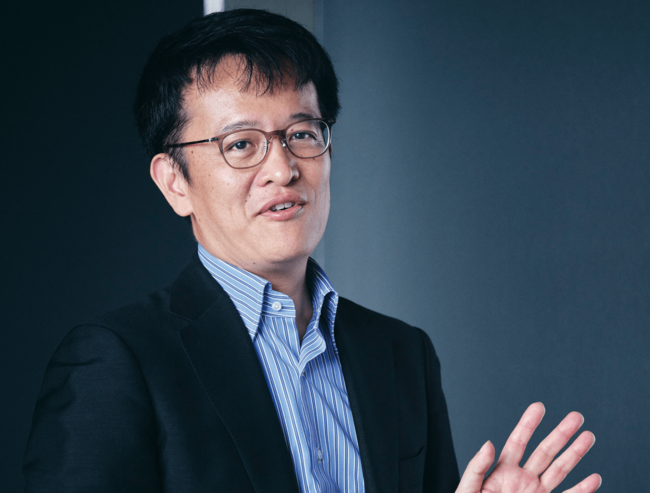
ターゲットは2030年です。24年の段階ではサプライヤーにポータルサイトから情報を入力・送信してもらい、メーカー側は統合基盤にデータを一元化する予定です。こうした仕組みは今後、多くの企業にとって欠かせないものとなります。
太田 上場企業は特に非財務情報の開示をステークホルダーから強く求められていますので、まさに不可欠なデータ共有基盤だと思います。
緊急事態対応情報に当たるBCP(事業継続計画)関連については、東日本大震災を経て当社でも情報共有の仕組みを整えましたが、環境や倫理に関連する情報共有はこれからで、まずはグループ内でデータを一元管理できる基盤を整備し、それを外部と連携させていくステップになると思います。
サプライヤー側からすると、いろいろなメーカーが互換性のないデータ共有基盤を構築してしまっては非効率ですし、社会的なコストも高くつきます。サステナビリティの実現は社会課題であり、非競争領域ですから、業界横断で標準化されたプラットフォームを開発していくことが必要です。
山中 日本でも約160社が加盟する「Green×Digitalコンソーシアム」が、サプライチェーン全体でCO2排出量を可視化するプラットフォームの検討を進めていますが、当社としては産業界共通の基盤構築に積極的に関わっていく方針です。
日本のものづくりをブラッシュアップするDX
山中 サプライチェーンDXは、産業全体の国際競争力や日本の経済安全保障に直結する重要課題でもあります。そうした観点から、太田さんの今後の抱負を聞かせてください。
太田 AGCはものづくりに強いこだわりを持っています。AGCだけでなく、日本のものづくりが、この先100年も国際的な存在意義を維持していくには、これからの10年が非常に大事だと思います。
長足の進歩を遂げるデジタル技術を活かし、日本のものづくりをいかにブラッシュアップしていくか。例えば、現場の足腰はしっかりしていますので、非競争領域における企業間連携が広がっていけば、日本は欧米に十分キャッチアップできるはずです。
実はいま、日本のいろいろなものづくり企業とDXについて議論を進めていまして、そうした企業と一緒に日本のものづくりをもり立てていきたいと思っています。
山中 われわれアビームコンサルティングのSCM(サプライチェーンマネジメント)セクターには500人ほどのメンバーがいます。グローバルに進出する日系企業の製造現場、物流現場に入り込み、日本のサプライチェーンに寄り添って規模を大きくしてきました。日系企業のものづくりの強みと課題は我がことのように理解しているつもりです。
個別企業レベルで競争力を高める段階から、規格化・標準化によって企業間連携を図り、産業エコシステムを構築する段階へと進むことで、日本のものづくりの強みをさらに磨き上げる道が開けると、私は確信しています。
アビームコンサルティング株式会社
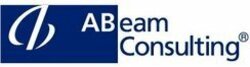
〒104-0028
東京都中央区八重洲二丁目2番1号
東京ミッドタウン八重洲 八重洲セントラルタワー
URL:https://www.abeam.com/jp/ja
アビームコンサルティングの知見や実践知を知ることができるスペシャルサイトを公開中
URL:https://promo.diamond.jp/gp/ad/sp-abeam/index.html