*〈前編〉はこちら
2019年に発生した新型コロナウイルスは、パンデミックへと拡大し、全世界に悲劇的なダメージをもたらし、その終息はまだ予断を許さない。そのような中、さまざまな事実や教訓が明らかになっている。
たとえば、グローバリゼーションの負の側面であり、デジタル技術のさらなる可能性と限界であり、歴史の知がなおざりにされているといった不幸な現実である。そして、大量の情報の氾濫を意味する「インフォデミック」の害は、非常に悩ましい問題である。実際、コロナウイルスの予防や治療、感染にまつわる情報には「根拠の怪しいもの」がかなり混じっており、しかも困ったことに、その真偽はしかるべき専門家に聞いて、初めてはっきりする。
ポストコロナの時代は大きく変わるとの見方がもっぱらだが、その具体的な方向性に関してはいまなお不確実な部分が多い。しかしすでに、明らかにバランスを欠いた処方箋が散見される。
ソーシャルメディアの普及によって、誰もが情報発信できる現在、こうしたインフォデミックがもたらす害悪はあらゆる領域で生じている。この事実を踏まえたうえで、前編に引き続き、日本製造業にまつわる根拠の怪しい論説について、まさしくしかるべき専門家である藤本隆宏氏に解説いただく。
地上のモノから発信されるデジタルデータは、IoT(モノのインターネット)を通じてすべてインターネット上のクラウドで処理され、地上のものづくり活動も上空からすべてコントロールできる。
デジタル化という支配的な流れの中で、産業用のIoTという言葉がよく聞かれるようになりました。先の3層モデル(前号13ページ)をいま一度引けば、「上空」のICTネットワークと「地上」の物財を、発信機付きのセンサーを通じて連結させることです。
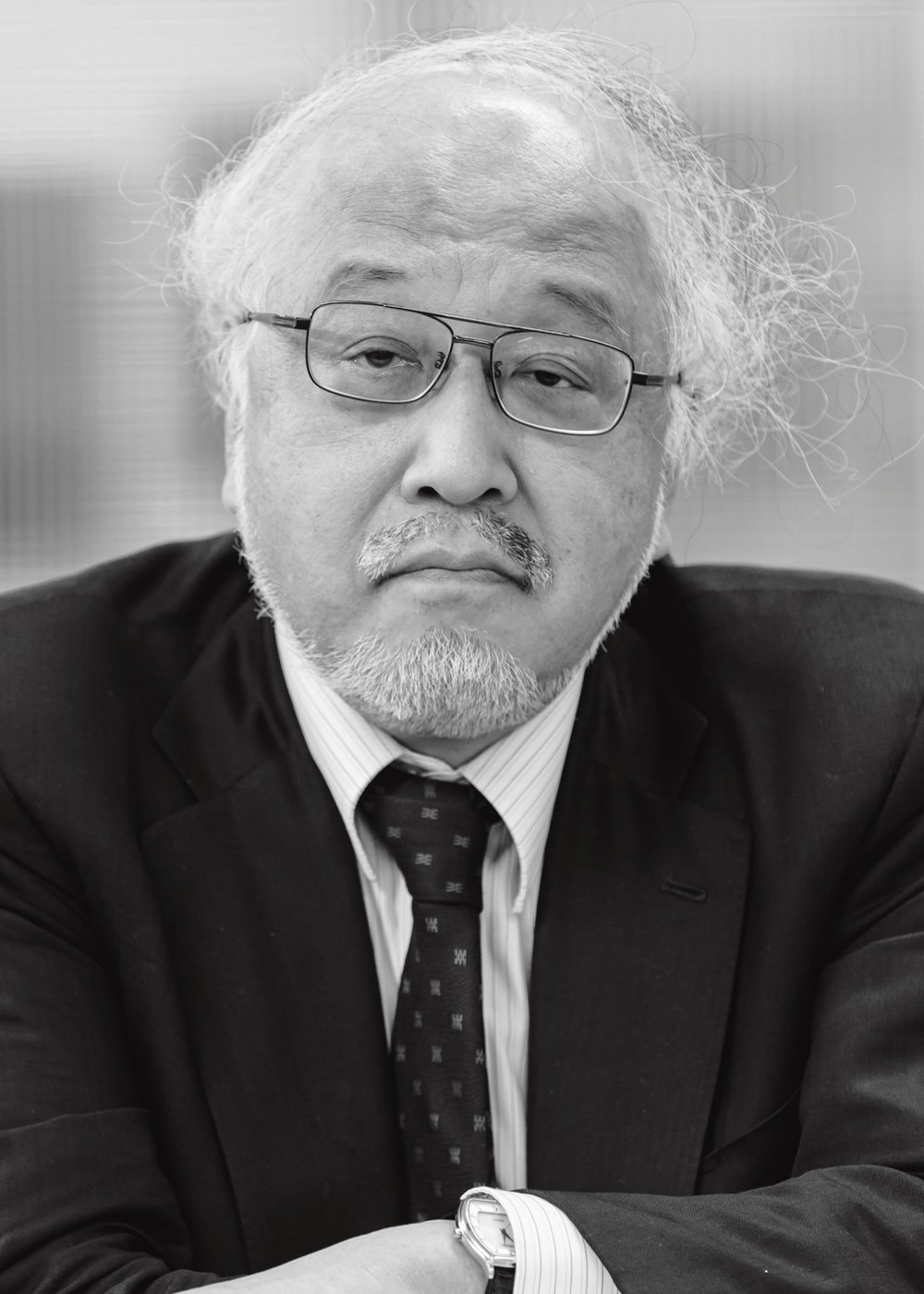
藤本隆宏 TAKAHIRO FUJIMOTO
東京大学大学院経済学研究科教授。東京大学経済学部卒業後、三菱総合研究所を経て、ハーバード・ビジネス・スクールにてDBA(経営学博士)を取得。東京大学経済学部助教授、1999年より現職。また、東京大学ものづくり経営研究センター長、一般社団法人ものづくり改善ネットワーク代表理事を兼ねる。主な著作に、『生産システムの進化論』(有斐閣、1997年)、『生産マネジメント入門〈1〉〈2〉』(日本経済新聞社、2001年)、『能力構築競争』(中公新書、2003年)、『日本のもの造り哲学』(日本経済新聞出版社、2004年)、『ものづくりからの復活』(日本経済新聞出版社、2012年)、『現場主義の競争戦略』(新潮新書、2013年)、『現場から見上げる企業戦略論』(KADOKAWA、2017年)が、共著に、『自動車産業21世紀へのシナリオ』(生産性出版、1994年)、『トヨタシステムの原点』(文眞堂、2001年)、『ビジネス・アーキテクチャ』(有斐閣、2001年)、『ものづくり経営学』(光文社、2007年)、『ホンダ生産システム』(文眞堂、2013年)、『ITを活かすものづくり』(日本経済新聞出版社、2015年)、『日本のものづくりの底力』(東洋経済新報社、2015年)、『ものづくりの反撃』(ちくま新書、2016年)、などがある。また、ハーバード・ビジネス・スクール学長(当時)のキム B. クラークとの共著Product Development Performance: Strategy, Organization, and Management in the World Auto Industry, Harvard Business School Press, 1991.(邦訳『製品開発力』ダイヤモンド社、1993年。増補版が2009年に発行)は、第35回日経・経済図書文化賞を受賞。
より具体的には、こうして収集された巨大なデジタルデータを、インターネット経由で上空のデータセンターのクラウドコンピューティングにつなげ、AIなどを活用してこれらのデータを分析し、その結果を地上や「低空」のユーザーや物財にフィードバックし、主に上空において巨額の利益と圧倒的な成長を得ようという構想です。
たしかに、生活空間にある消費財やサービスの需給や売買といった「マッチング」の世界では、アマゾン・ドットコムを先頭に、インターネットビジネスのプラットフォーマーは絶大な力を発揮してきました。
一方、自動車や工場の設備などに対する、高速かつ精密な「コントロール」の世界になると、これまでの(いわゆる5G以前の)インターネットは、その伝送速度に限界がありました。つまりリアルタイム性の不足で、インターネットでは通信が遅れてしまう。そこで、その他のタイプのネットワーク、たとえば車載通信ならばコントローラーエリアネットワーク(CAN)、工場内の設備制御ならばリアルタイム性を重視したフィールドネットワーク(フィールドバスとも)など、インターネット以外の専用線ネットワークが併用されてきました。つまり、そうした高速かつ精密な自動制御(コントロール)は、インターネットだけでなく、あらゆる通信ネットワークを総動員することで、何とかこなしてきたわけです。
たとえば、プレス機に発信機付きセンサーをつけ、仕掛品に異常が発見された場合には、加工の前に自動で機械を止める、というシステムを導入した工場があります。これもIoTと呼ばれています。ただし、この場合、センサーと生産設備の間にあるのはフィールドネットワークで、インターネットを介在していません。とすれば、この実態を表す言葉として、IoTはちょっとおかしいですね。
つまり、自動車や工場など、高速かつ精密な自動制御の世界では、IoTという言葉はあまり適切ではありません。むしろ「IfT」(Information from Things)、つまり発信機付きセンサーをモノにつけて「現場のモノから情報を得る」という言い方のほうが、実態をより正しく反映しています。
いずれにせよ、近年、日本の工場におけるIoT/IfTの傾向を見て気づくのは、個別設備の稼働率を向上させるための「予知保全」の例が非常に多いことです。2019年、私のゼミの学生が、ものづくり系の専門誌に掲載された工場内でのIoT活用事例を、予知保全(故障予測)、予知品質管理(不良予測)、予知生産管理(仕掛品の渋滞予測等)の3つに分けて集計したところ、実に半分近くが予知保全でした。
予知保全の重要性を否定するつもりは毛頭ありませんが、それが実施事例の半分近いというのは、いくら何でも多すぎるという印象を受けました。予知保全は、基本的に個別設備の稼働率を向上させる方策であり、その意味で、部分最適指向だからです。トヨタ生産方式やTOC(制約条件の理論)でもいわれるように、ボトルネックではない設備の稼働率を上げても、仕掛品の流れの全体最適には結び付きません。
実際、個別設備の稼働率は向上しても、工場やサプライチェーン全体としては「仕掛品の渋滞」、ひいては生産リードタイムの長期化を引き起こしてしまうかもしれません。車間の詰まった高速道路で、ドライバーたちがいっせいにアクセルを踏めば、そのせいで大渋滞が発生するという話と似ています。その昔にお会いした、トヨタ生産方式の生みの親、大野耐一さんがご存命であれば、「ボトルネックでもないところの稼働率を上げて何が面白いんだ」とおっしゃることでしょう。
それよりも私がいま見たいのは、たとえば工場内のコックピット(大型モニター)で、工場全体の仕掛品の流れと全設備の稼働状況、できれば主要サプライヤーのそれらもリアルタイムで一覧できる、広域現場の「流れ」のサイバーフィジカルシステム(CPS)です。これがあれば、「多能工のチームワーク」を持ち味とする日本の統合型の優良現場ならば、モニターを見ていた現場の人たち自身が「これは30分以内に下流で渋滞が発生するぞ。いまはうちの設備の稼働率を上げている場合じゃない。2~3人、あっちの応援に行ってこい」と、広範囲の助け合いを始める可能性が大です。
こうした「広域の連携調整」による流れ改善は、中国や欧米の工場よりも、もともと調整型・統合型である日本の優良工場でこそ多く見られます。ただし、こうした広域の「流れ」を即時に把握するCPSは、膨大な通信と情報処理を必要とするかもしれません。劇的に遅延が減る5G技術を工場内で使う「ローカル5G」、論理構造の推定などに適するとされる量子コンピュータとAIの併用などを含め、最先端の現場では、新しいICTが総動員されるようになるかもしれません。