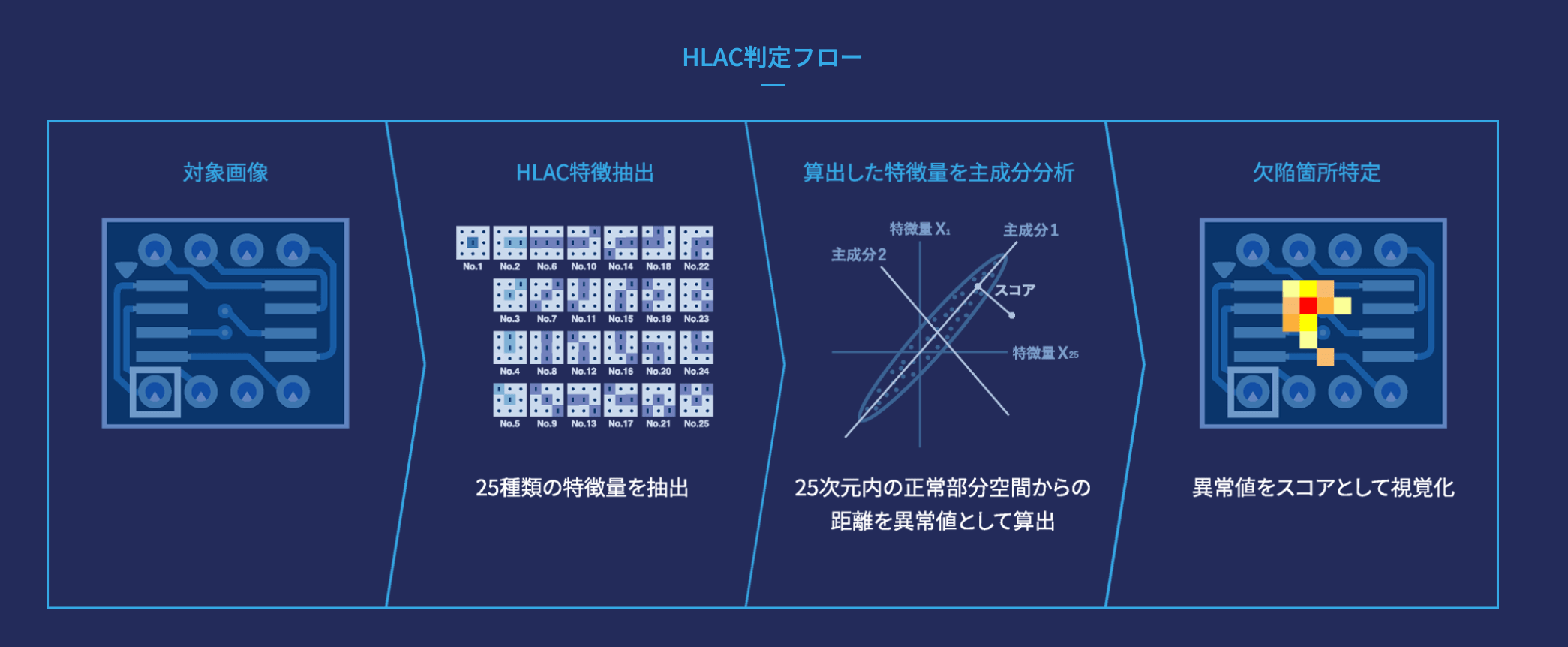
アダコテックの顧客となるのは主に大手メーカーの生産技術部だ。その顧客に対してAIの学習モデルを構築するためのアプリケーション「AdaInspector Cloud」と、現場でカメラと接続してAIを動かすためのアプリケーションをセットで提供している。
大手企業向けプロダクトのため実証実験を経て正式導入に至るケースが多いが、ソフトウェアの提供企業数は累計で150社近くまで増えてきた。河邑氏によると特にこの1年でその数が約100社増加するなど、事業に対する手応えを感じられるようになってきたという。
プロダクトの価格は企業規模や利用用途などにもよるが、年間でだいたい300万円ほどから。今年度は数億円規模の売り上げを見込んでいる。
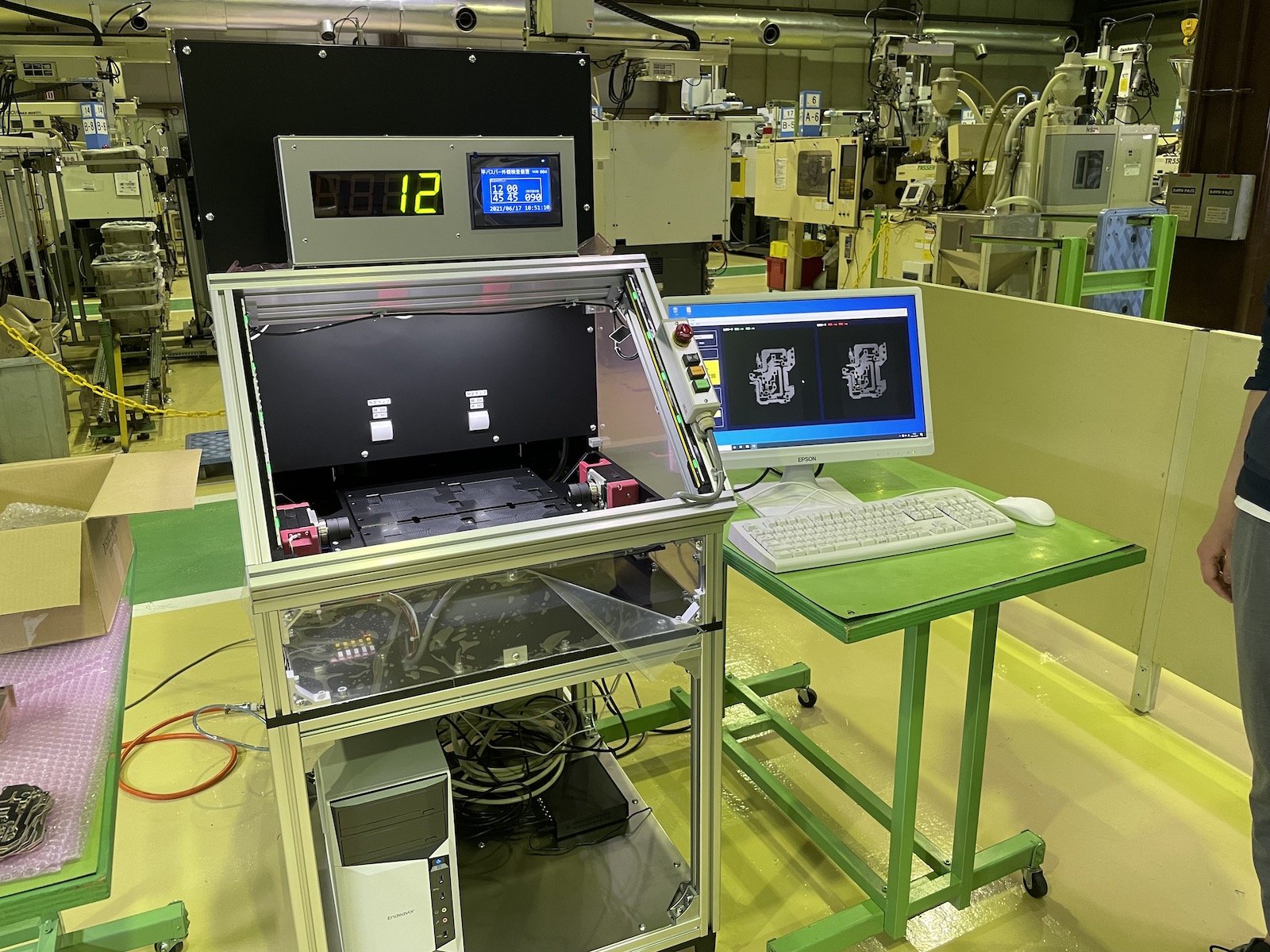
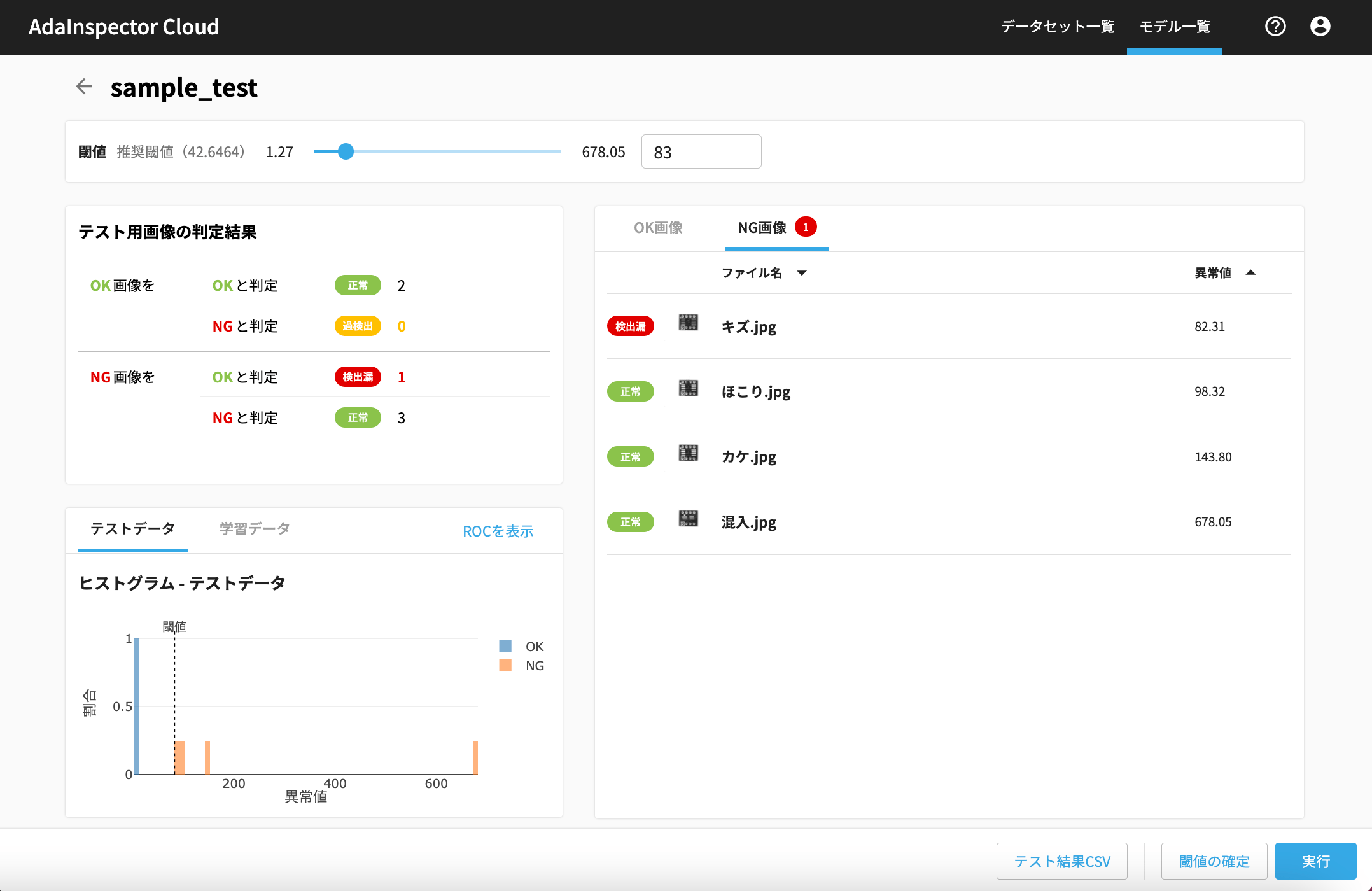
140社以上にソフトウェアを提供、本田技研工業との共同実証も
山梨県に本社を構える部品メーカーでは、自動車部品の外観検査においてアダコテックのソフトウェアを活用している。
部品の製造工程において生じる傷や打痕などの欠陥は数ミリと細かく、その種類や場所も多岐にわたることからシステムでの検出が難しいことから、熟練者が目視で検査してきた領域だ。
ただ部品の需要が増す中で検査のキャパシティがネックとなり、機会損失が発生してしまうという状況に陥った。そこで人不足や技術の継承難といった課題の解決策にもなりうることから、アダコテックのシステムを活用することを決断。導入後は検査時間が約3分の1程度に短縮され、4人がかりで担当していた業務が1人でも対応できるようになったという。
「検査は固定コストになってしまうので、毎月必ず同じ量だけ生産するのであれば人で良いという企業もありますが、製造量に波が出てくると人が浮いてしまいます。その点も自動化によるメリットの1つです」(河邑氏)
このメーカーの場合は河邑氏自身が現地に1週間泊まり込み、実際に工場での目視検査業務を体験しながら課題のヒアリングやサービスの提案を行った。ここまでするケースはさすがに珍しいというが、アダコテックでは現場への訪問を重要視しており、それがプロダクトの発展や事業の成長にも結びついてきていると話す。
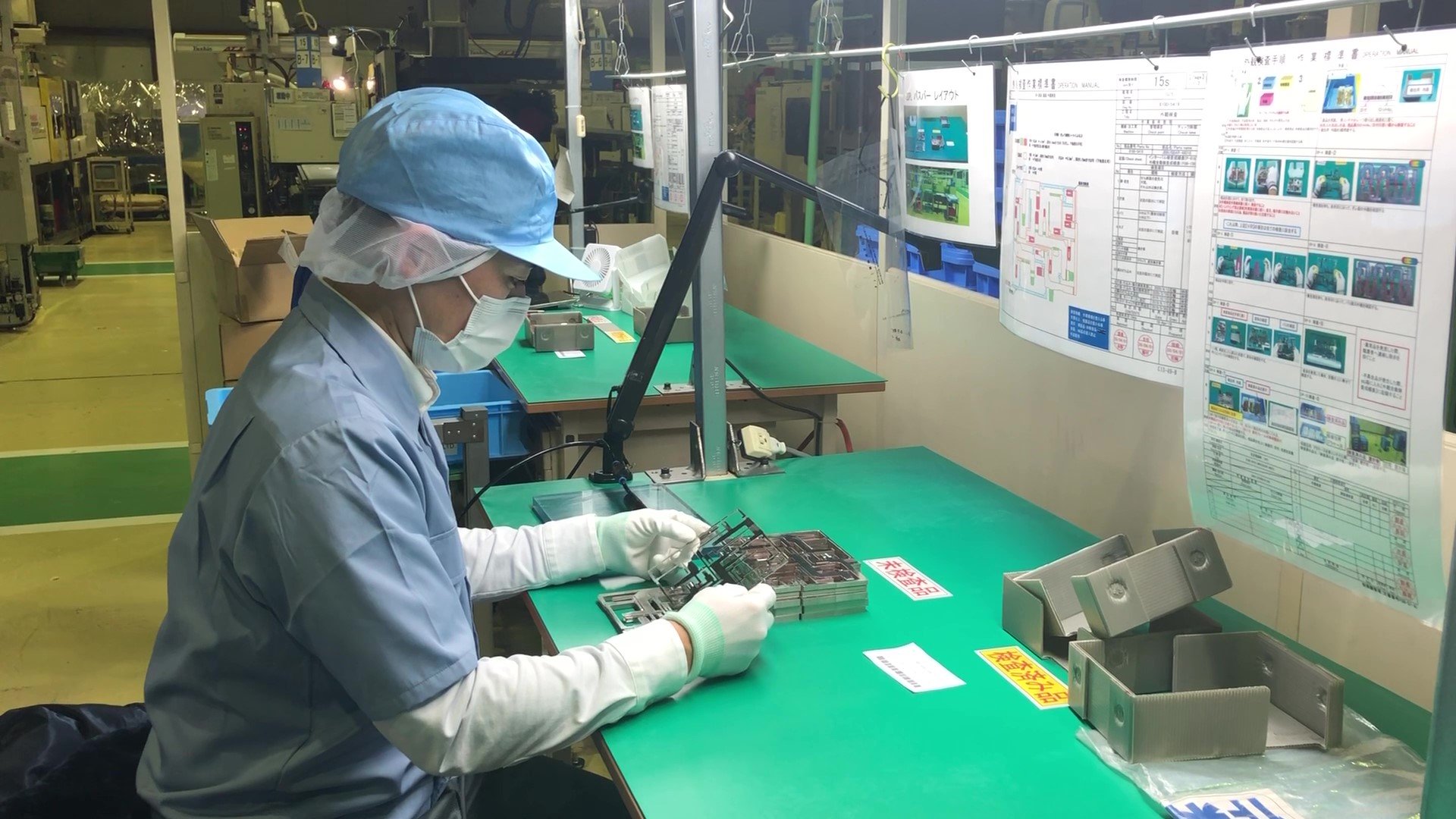
別の自動車部品メーカーではアダコテックのシステムを活用することで21人だった検査人員が12人に減り、別の業務に人の力を生かせるようになった。検品のデータ化が進み良品率も93%から96%へと改善された結果、1つの工場の1つの工程を変えるだけで年間2.3億円の導入効果が見込めるといったような事例も生まれている。