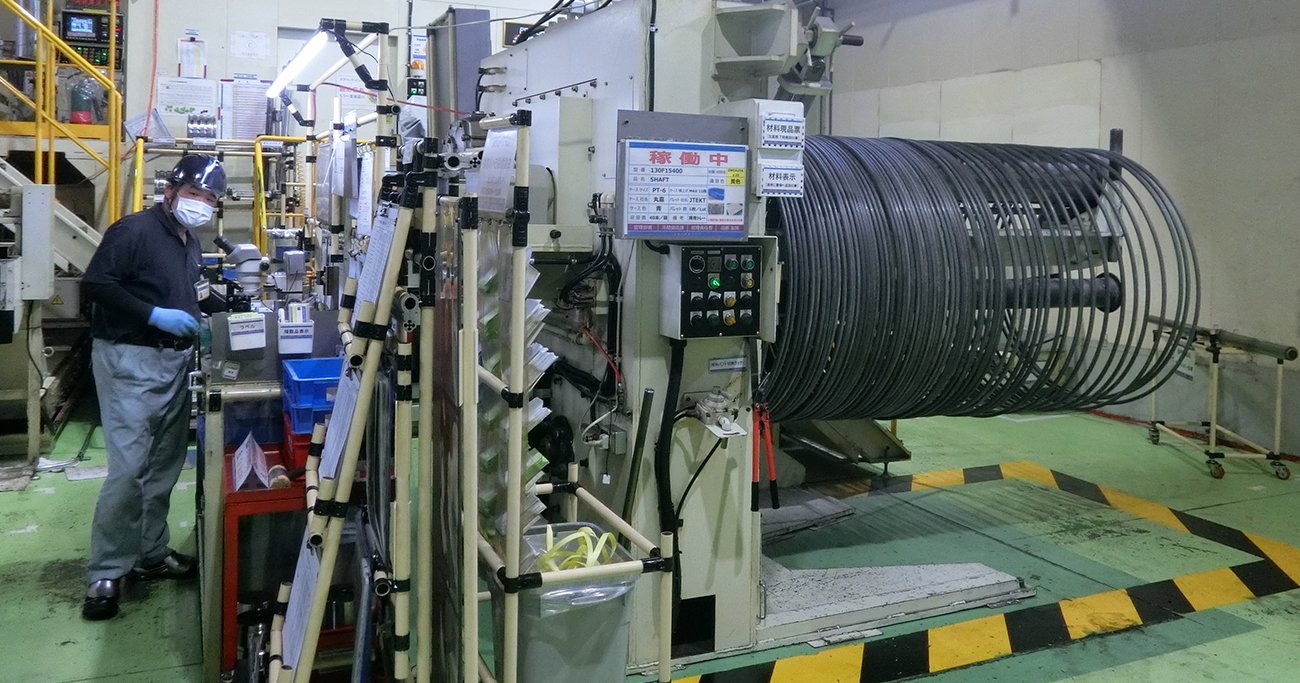
目指すは「冷間鍛造技術日本一」――そんなスローガンの下、あえてハードルの高い技術開発に果敢にチャレンジ。素材成形から組み立てまで手がける一貫生産体制で、自動車関連部品をはじめ高精度な製品でものづくり産業を支える企業がある。岐阜県各務原市の丸嘉工業だ。(取材・文/大沢玲子)
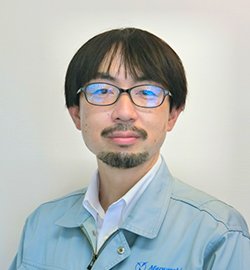
同社は1959年に創業。カーボン軸受生産からスタートし、多種多様なベアリングの他、車のトランスミッション・ステアリングシステム部品といった自動車関連部品、工作機械のサーボモーター用スピンドルなどの電機関連部品にも市場を広げ、中国にも生産拠点を設置。長年培ってきた独自の機械加工および組み立て技術で、幅広い分野の顧客ニーズに応えてきた。
しかし、製造業において一層のコスト削減や部品の軽量化などが求められる中、「機械加工前の素形材の鍛造プロセスを手がけ、さらに付加価値の高い一貫生産体制を構築すべく、冷間鍛造の技術開発に乗り出すこととなりました」。2020年より同社代表取締役社長を務める土田雄一郎氏はそう語る。
冷間鍛造技術の中でも
難しい加工にこだわる
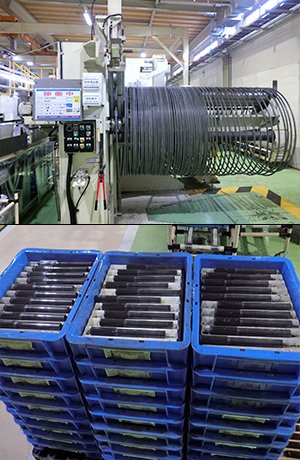
冷間鍛造とは、金型を用いて常温の状態で金属などに圧力を加え、目的の形状に成形する加工技術を指す。加圧によって金属の内部組織が緻密で均質になるため、強度、硬度などの機械的性質が改善。さらに目的の形状に成形されるため機械加工が省略でき、最小限の材料で加工が可能。コスト削減につながるなどのメリットがある。
同社が冷間鍛造に乗り出すため冷間鍛造設備の「パーツフォーマ」を導入したのは03年のこと。冷間鍛造メーカーとしては後発に当たる。
「最初から、他社には追随できないような困難な技術を確立しようと開発をスタートさせました」(土田氏)
適切な金型の調整をはじめ、当初は試行錯誤の連続で、収益が出る事業として確立するまでには約10年もの年月が必要だったという。では、丸嘉工業ならではの冷間鍛造技術の特徴はどこにあるのか。