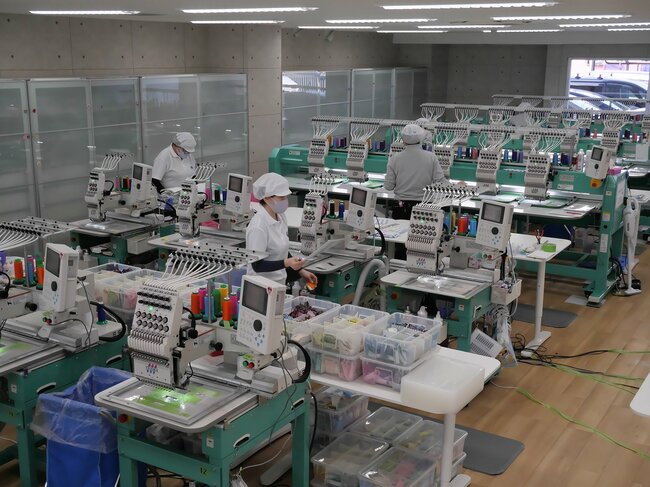
中小企業の生産性向上と経営課題の解決のためにはデジタルシフトによるDX(デジタルトランスフォーメーション)が必要と叫ばれて久しいが、まだ取り組み状況には濃淡がある。そんな中、刺しゅう加工会社のミノダは、社内の問題解決に向けてDXに取り組んできた。どんな成果があったのか、箕田順一社長に聞いた。(取材・文/ダイヤモンド社 ヴァーティカルメディア編集部 大根田康介、撮影/瀧本清)
「下請け加工業では食えない」
危機感から新規事業を立ち上げた
刺しゅうワッペンを製作する刺しゅう加工メーカーであるミノダは1964年、現社長の箕田順一氏の父が東京都千代田区岩本町で創業した。
箕田順一氏が高校生の時、父が亡くなり、母が事業を継いだ。
「昔はスーツに個人ネームを刺しゅう加工するには高い職人技術が必要で、母にその技術があり、何とか生計を立てられた」と箕田社長は回顧する。
その後、同社は企業向けに作業服などへ刺しゅうを施す事業を手掛けてきたが、一方で顧客であるアパレルメーカーが海外生産に移行。機械化も相まって、刺しゅう加工業の低賃金化が顕著となり、同社はビジネスモデルの転換に迫られた。
そんな中、2004年に箕田順一氏が社長に就任。箕田社長は「もはや下請け加工業だけでは食っていけない」と危機感を覚えていたことから、基幹のEMB事業部(刺しゅう加工事業)に加え、ホビー事業部(キャラクター商品の販売事業)、通販事業部(一般個人向けのEC事業)を立ち上げた。
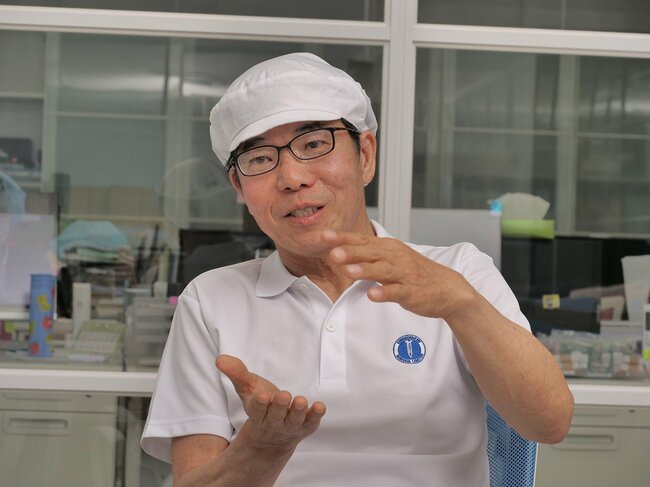
新しい道を歩みだした同社だが、そこには多くの困難が待ち受けていた。DXにより、どうやって難問を解決していったのか。