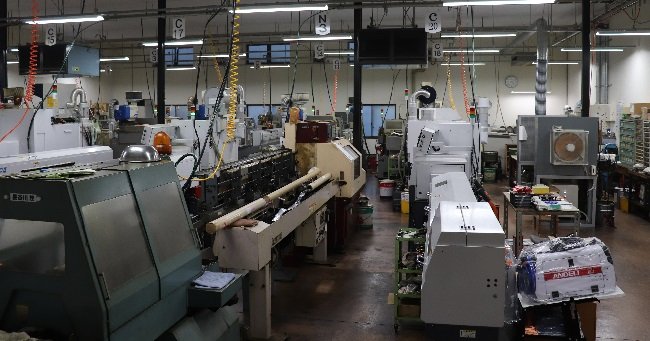
――御社の事業内容を教えてください。
鈴木 内視鏡関連の医療機器や光学機器、自動車部品といった精密機器の部品を、主軸移動型の精密自動旋盤で切削加工し、製造しています。
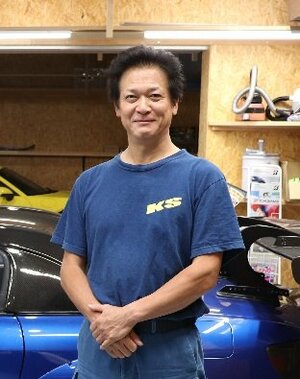
これらの部品に共通するのは直径3ミリメートル以下の小径部品であること。数ミクロン単位の寸法精度が要求され、バリ(加工で生じる突起)が許されないなど、超精密加工が要求されるので、製造できる企業はかなり限られます。それができ、かつ量産できることが弊社の強みです。
今では「小径部品の量産は金鈴精工」というイメージが浸透し、競合他社さんから「金鈴精工ならできる」と紹介されることもよくあります。
――創業当初から精密加工の仕事をされていたのですか?
鈴木 もともとは明治時代に創業した機屋でした。地元・青梅は機織物の生産が盛んだったエリア。弊社は地域で2番目に古い機屋で、一時は住み込みの女子工員さんが40人近くいたそうです。
しかし、時代の流れには逆らえず、1960年代になると機織物の需要がなくなってしまいました。そのとき、奥多摩にある主軸移動型の精密自動旋盤のメーカーが急成長していたのを見て、私の父がその機械を購入して精密加工業にも進出したのです。弊社だけでなく多くの機屋が同業に転じました。
――そこからどう発展を?
鈴木 しばらくはカーオーディオ部品を製造していましたが、私が専務になった90年代に、中国が大規模生産設備と人件費の安さで“世界の工場”として台頭してきて、カーオーディオの仕事を奪っていきました。中国と生産力や価格で勝負しても勝てないと、大半の同業者は多品種・小ロット・短納期に活路を見出そうとしました。
しかし私は、その逆の「大量生産」にかじを切りました。複数の機械を用意してそれを1人のオペレーターで回せば、中国との人件費の差はつきにくい、と考えたのです。もちろん、どこでも加工できる簡単な部品では中国に勝てませんが、他社が断るような3ミリメートル以下の部品なら勝ち目はある。そう考えて、小径部品用の機械ばかり増やしてきました。
――それが当たったわけですね。
鈴木 90年代には技術の進歩でさまざまなデジタル関連製品が次々と生まれました。この時代の流れに乗り、それらの製品の小径部品を着実に受注できるようになりました。コンパクトカメラに始まり、2000年代にはデジタルカメラや携帯電話部品など、単一部品の生産で最高月産120万個になりました。その実績が買われ、より難易度の高い光ファイバーコネクタやHDDシャフトを毎月100万個以上製造するようになりました。