メーカー(製造業)では自動車、電機、食品……などの商品をつくって売る「ものづくり」が仕事です。それを支えるさまざまな機能がありますが、「製造技術課」とは一体どんな仕事なのか、また「V型やA型といった製造工程」の違いは何か、そして、「VATI分析」とは何か…など、メーカーを目指す人ならぜひ知っておきたい基本について、書籍『全図解メーカーの仕事 需要予測・商品開発・在庫管理・生産管理・ロジスティクスのしくみ』から紹介していきます。
ものづくりを担当する「製造課」に対し、「生産技術課」の仕事とは?
工場の現場でものづくりを担当しているのは「製造課」(注:企業によって名称が異なる場合もある)の人々ですが、製品をどのような手順で作るのかといった製造工程の設計や、ものづくりのための生産設備そのものを製作するのは「生産技術課」の仕事です。
生産技術課は、デザイン通りの製品を量産するための方法を考えると同時に、メーカーとして儲けを十分に出せるような、効率的な作り方の手順や道具を考えることをミッションとしています。そのため、生産技術課の仕事にはエンジニアとしての優れた知見や技能だけでなく、「製造課の誰がどのような技能をもっているか」「生産設備にはどのようなクセや能力があるか」「製品を構成する原材料はどのような特性があるか」といった、製造工程についてのあらゆる情報に精通していることが求められます。生産技術課はメーカーにとって不可欠なものづくりのプロ集団といえるでしょう。
生産技術課の日々の仕事には、稼働中の製造工程や生産設備のメンテナンス、新しく導入する生産設備や製造工程の設計、新商品の品質評価基準の策定、外部から調達する原材料の性能評価などがあります。これらの仕事は製造課、購買課、品質管理課、生産管理課とお互いの情報を頻繁に交換しながら進めることになります。
また、複数の工場を持つメーカーでは各工場の工程設計だけでなく、工場間のものづくりの連携についても設計する必要があります。このような場合、各工場の生産技術に関する仕事を統括する部門が設置され、この部門に所属するエンジニアが各工場を巡回、または各工場に駐在するなどして前出の仕事にあたることになります。
想定通りにいかない稼働状況
生産技術課は、製造工程をデザインする際に需要予測や原材料の入手性、および各工程(ショップ)の処理能力など考慮して、工場全体のものの流れ(フロー)が滞りなく進むことを目指します。
しかし、継続的に生産を続けているうちに当初予定していたようなフローで生産が進まなくなることがあります。例えば、同時に部品8個を作ることができるように設計した金型が、いつの間にか老朽化して4個しか作ることができなくなっている、設備の入れ替えで生産能力が高くなったことで現場が張り切ってたくさん作りすぎていた、といった場合などがこれにあたります。
まさか、と思われるかもしれませんが、ものづくりの現場である個々の工程を担当する製造課のメンバーは、持ち場のオペレーションに集中することが求められるため、手元で起きた変化が工場全体にどのような影響を与えるのか把握することは実は困難なのです。
工程の生産能力が低下したことが工場全体に知られていないことで、この工程には前の工程から送られてきた仕掛品が処理しきれないまま山積みになります。反対に、工程の生産能力が向上したことを工場全体に知らせずに作業を続ければ、後ろの工程に仕掛品の山を作ることになるのです。このように製造工程のどこかで工程の処理能力を超えてしまう状況になると、処理能力に余裕のある工程が単独で頑張っても工場全体としての生産量を増やすことはできません。
この工場全体のもののフローを制約している工程はボトルネックとよばれます(図8-2)。ボトルネックを発見するのは、「鳥の目」で工場全体のものの流れを把握している生産技術課に求められる役割であり、もしも発見した場合はただちに過不足のないように製造工程を見直すことになります。
また、まだボトルネックになってはいないものの、もうすぐ能力の上限に達しそうな工程に目を光らせて、先手を打っていくのも生産技術課の重要な役割です。
ものづくりの現場である工場は、細分化された加工作業を受けもつ工程の組み合わせで構成されています。この組み合わせは工場で生産する商品の特徴によっても異なりますが、おおむね次のように整理することができます(図8-3)。
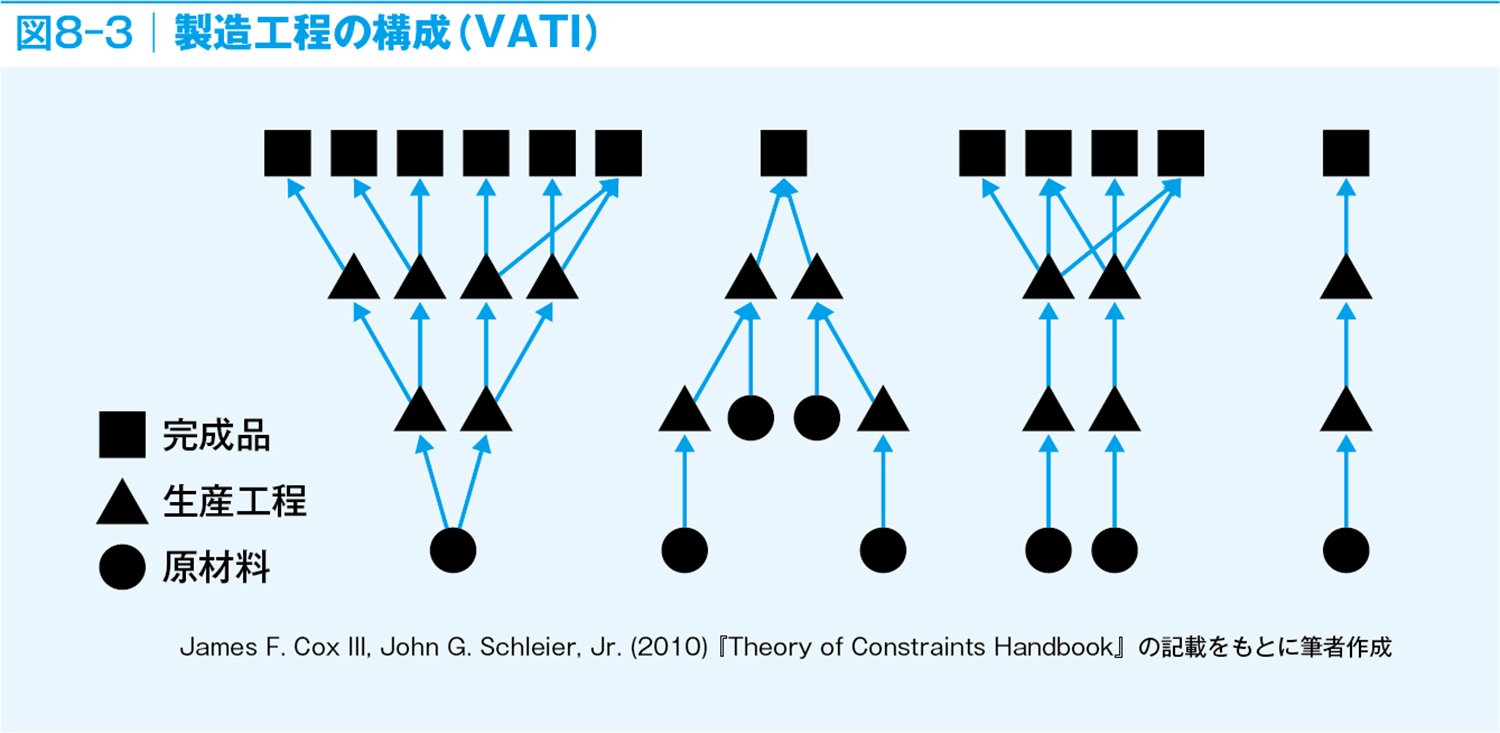
拡大画像表示
●A型の製造工程:複数の原材料から一つの商品を加工する構成の製造工程(鉛筆:木材→軸板+黒鉛&粘土→芯)
●T型の製造工程:複数の原材料から同数の中間品を作り、その組み合わせや加工によって複数の商品を作る構成の製造工程(パソコン:外装×CPU×メモリ×SSD×キーボード×ディスプレイ×電源)
●I型の製造工程:1種類の原材料を1種類の商品に加工する構成の製造工程(シンバル:青銅→シンバル)
このように原材料を起点とする工場内のものの流れに沿って製造工程の構成を整理・分析するアプローチは「VATI分析(VATI Analysis)」として知られており、特に工場全体の供給能力を制約しているボトルネック工程を発見するための手法として用いられます。また、このボトルネック工程の処理能力を基準として工場全体の生産能力を管理する考え方は「TOC(Theory of Constraints:制約理論)」として知られています。
*さらに詳しく知りたい方向けには、『全図解メーカーの仕事』に参考文献リストも掲載しています!