チョウが描いた図の上に、麻理は異なる工程ごとに色づけをしていった。大きく分けると、全部で10工程ほどあることがわかった。
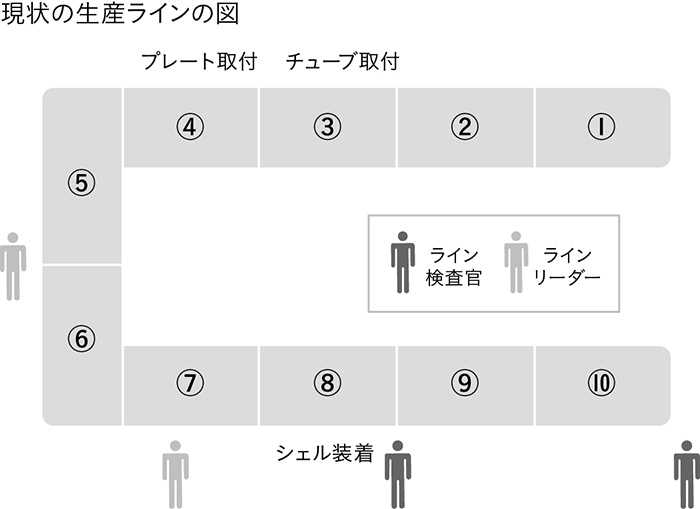
この図を見ながら、麻理はチョウに質問した。
「これらの各工程で、品質の確認はしているのでしょうか」
「組立や溶接に失敗した場合は、すぐにラインから取り除いているよ」
「それは何か明確な基準があるのですか、それとも各担当者が個別に判断しているのですか」
「特に基準は設けていないけど、ラインの担当者は自分で作っているんだから、良いか悪いかはすぐわかるよ」
「わかりました。それでは、出荷前の最終検査はどのように行っているのですか」
「冷却性能については、全品検査しているよ。静音性能については、抜き取りのサンプル調査だが、静音ルームのキャパシティーが不足しているので、実際はあまり検査できていないな」
「状況はわかりました。それでは、不良品が発生する原因を地道に究明しましょう!」
麻理は確信を得たように言い放った。
モデルラインの導入
翌日健太と麻理は、総経理のスティーブ、副工場長のチョウ、開発担当の山田、そして瀬戸の4名を大会議室に招き、生産品質の改善について話し合うことにした。
瀬戸は部屋に入るなり、「このメンバーでいいのかな?」と質問した。
それに対して麻理は、「不良率の高さは生産プロセスの問題だと思いますので、まずはこのメンバーで対策を話し合いたいと思います」と答えた。
その言葉に、一同はテーブルを囲むように着席した。
麻理はこう切り出した。
「今直面している不良率の高さの問題は、何が不良の原因かがわかっていないことです。出荷前の検査では、静音性能はほぼノーチェックです。冷却性能は全数を確認していますが、客先からは要求水準に届かず返品されたものが数多くあります。つまり、我々は作ったものをきちんと確認もせず顧客に出荷し、それが2~3ヵ月後に客先検査で引っかかり、返品されるという繰り返しになっています。返品された製品は、ごく一部だけがその原因を解明され、さらに再利用されているのはそのうちの一部となっています」
健太は麻理の的確なコメントに大きく頷いた。
〈しかし、どうやって不良率の原因を突き止めるか、それが問題だ〉