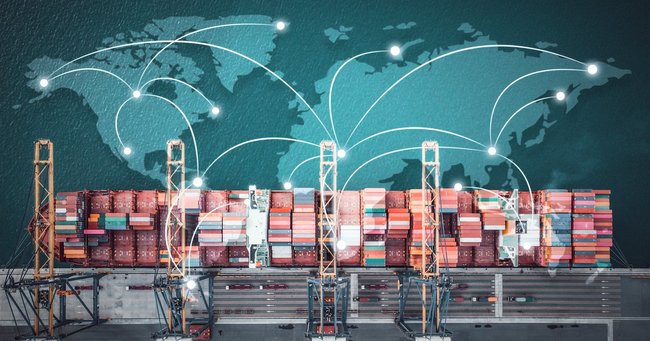
新型コロナウイルスは製造業に大きな爪痕を残した。大規模に感染が拡大した中国では都市封鎖を実施したため、あらゆる企業が製造や供給をストップ。部品の製造や供給などのサプライチェーン(製品供給網)を中国企業に依存している世界中の製造業は、大打撃を受けた。日本の製造業はこうした事態をどのように乗り切ればよかったのか。今後訪れるであろうコロナ感染の第2波、第3波に対して、どのように備えればよいのか。製造業のサプライチェーン構築に関するコンサルティングを行っているアクセンチュアの2人の専門家に話を聞いた。(聞き手/ダイヤモンド編集部 片田江康男)
生産拠点の複数化と
部品の複数社発注が重要
――コロナ禍によって中国の製造工場や部品の供給元の稼働が止まり、日本の製造業はサプライチェーン(製品供給網)が寸断されました。製造業のサプライチェーンの構築・改善を専門にコンサルティングをされていますが、この半年をどのように見ていましたか。
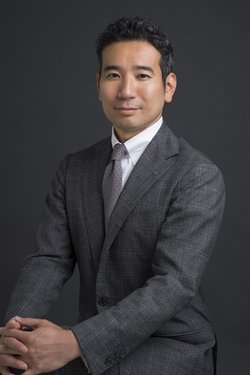
太田氏 比較的冷静に見ていました。当社のクライアント企業も同じで、特に混乱するわけでもなく、冷静でした。ただ、全世界が一斉にクラッシュするのは想定していませんでしたので、ある意味、諦めに近い心境だったと思います。
――サプライチェーンの見直しなどは行う必要があるのでしょうか。
太田氏 いえ、必ずしもそうではありません。というのも、私たちは2008年のリーマンショック、11年の東日本大震災にタイの洪水と、ここ10年間で3回の困難を経験しています。
その経験から、自動車業界などは生産拠点を複数持つことや、部品を複数社に発注して調達するなどの対策を進めてきました。自動車の完成車メーカーは、電機メーカーなどと比べて部品供給元などのサプライチェーンをコントロールする力が強いので、そういった対応はかなりできているという印象です。
ただ、今回のコロナ禍では、全世界が一斉に止まってしまったので、これまでの対策で対応可能だったかどうかは、評価が非常に難しいと思います。リプランしても防げるかどうか……。
やるべきこととしては、複数生産拠点化や部品の複数社発注ができていない企業はそれを急ぐということでしょう。すでにできているところは、危機対応力を上げるということじゃないでしょうか。