メーカー(製造業)の仕事は、自動車、電機、食品……などの商品・サービスをつくって売ることですが、お客さまに満足いただけるものを過不足なくつくって遅滞なく届けるために、メーカーにはさまざまな機能があります。たとえばお客さまに過不足なく届けるために不可欠な「在庫」ですが、これを持つためにはさまざまなコストがかかることをご存じでしょうか。メーカーを目指す人なら知っておきたい基本について、書籍『全図解メーカーの仕事 需要予測・商品開発・在庫管理・生産管理・ロジスティクスのしくみ』から紹介していきます。
在庫をもつことで、メーカーにはさまざまなコストが発生します。
具体的には次のようなコストがあります。
●購入コスト:原材料や製品を購入する費用。単価×数量分のコストが発生する。
●保管コスト:倉庫の使用、荷役(貨物を出し入れする際などの作業)人員、装置の維持、使用等に対する費用。
●発注コスト、輸送コスト:発注するために必要な費用や、原材料や製品を輸送するための費用。発注する際の事務的な手続きや、発注後のオーダー管理にかかる費用も含む。発注後のオーダー管理とは、発注してからも希望納期通りに納入されるかを確認することや入荷してからの支払管理等を指す。発注頻度を増やせば増やすほど、1回当たりの入荷数量を減らすことができるが、発注コストや輸送コストは増加する。
●廃棄コスト:使用期限切れや廃番に伴い、製品を廃棄するためにかかる費用。在庫を必要以上に多くもってしまうと、しばらく販売、出荷されない滞留在庫が増え、結果として廃棄コストが増えてしまう。
●販売機会損失コスト、顧客損失コスト:品切れしてバックオーダーが発生してしまうと、販売機会の損失や、顧客を失うリスクが発生する。これを金額で割り出すのは難しいが、顧客からの発注に対する、希望納期達成率で測定される。これは、顧客が望む納期に間に合わなかった分は機会損失と捉えると同時に、顧客満足度を損なっている、という考え方である。ほかにも、品切れによって下降した売り上げ分を機会損失とするメーカーもあるが、品切れ解消後にその分の売り上げが上がる場合もあり、機会損失を定量的に評価するのは難しいといわれている。
在庫管理では、これらコストのバランスを見ながら、発注単位・発注タイミング・発注頻度を決めることになります。
図11-1は、在庫関連コストのトレードオフを示した概略図になります。1回当たりの発注数量が大きくなるほど発注コストは下がりますが、逆に保管コストは保管スペースがより必要になるため大きくなります。
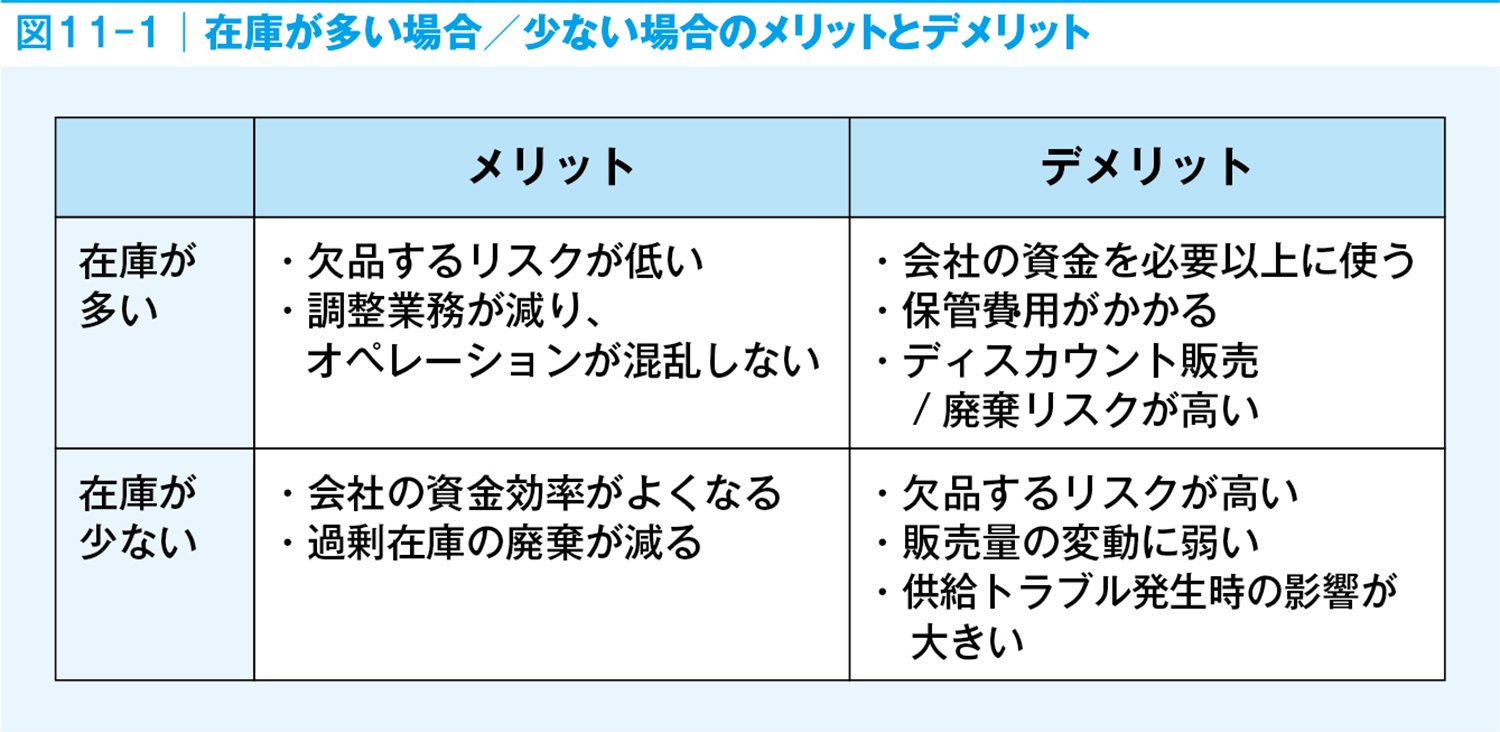
拡大画像表示
また、一度に必要な数量以上のものを購入してしまうと使用期限切れなどによる廃棄コストも大きくなります。そのため総コストはある数量で最小となり、それ以上になると大きくなっていきます。
ある消費財メーカーでは、需要予測が小さい製品の受注単位(小売店や卸卸売業者からの発注単位)を小さくする、といった工夫を行っています。あまり売れない商品の受注単位を大きくしてしまうと、店舗での売れ残りが発生し、それはいずれ、返品として戻ってくる可能性が高くなるからです。この場合、発注コストを含めた総コストは高くなる可能性があり、そのバランスを考慮することが必要です。